Placer Gold Mining: From Exploration to Plant Equipment Configuration
Placer gold mining involves excavating gold-bearing alluvial deposits (gravels, sands) and using gravity-based methods to concentrate the naturally freed gold particles. Success hinges on thorough assessment and optimized processing.
What is Placer Gold? How Does it Fundamentally Differ from Lode Gold?
Placer gold is gold naturally eroded from its original source (lode deposit) and redeposited in sediments like riverbeds or beaches. Unlike lode gold requiring drilling/blasting/crushing, placer gold particles are typically free and mixed with gravel/sand.
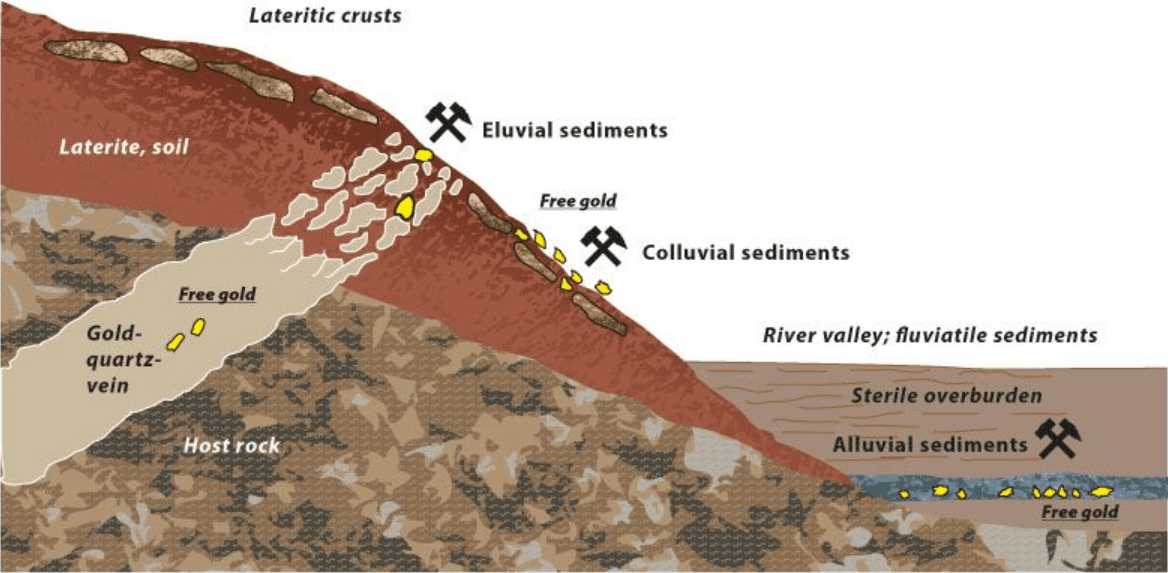
Understanding Placer Deposits
The key difference lies in formation and extraction:
Origin Story
- Source: Placer gold originates from primary lode deposits (veins, disseminated gold in rock).
- Weathering & Transport: Over geological time, weathering breaks down the host rock. Erosion (primarily by water, sometimes wind or glaciers) transports the debris.
- Concentration: Because gold is very dense (heavy), it settles faster than lighter sand and gravel during transport, concentrating naturally in specific locations like river bends, behind obstructions, or on bedrock.
Common Placer Types
- Alluvial Placers: Found in present or ancient riverbeds, floodplains, terraces. Most common type.
- Eluvial Placers: Formed on hillsides near the source vein, minimal transport.
- Bench Placers: Ancient river deposits left high and dry as the river cuts deeper.
- Beach Placers: Concentrated by wave action along coastlines.
Why Simpler Processing?
- Natural Liberation: The gold particles are already freed from the host rock by natural processes.
- No Crushing/Grinding Needed: Eliminates the need for expensive and energy-intensive crushing and grinding circuits typical of lode gold mining.
- Gravity is Key: Recovery relies primarily on the density difference between gold and lighter gravels, using relatively simple water-based gravity separation techniques.
- Insight: This generally leads to lower initial investment (CAPEX) and simpler processing flowsheets compared to hard rock operations, making it attractive for smaller-scale miners. However, efficiency still requires careful design.
How Can We Scientifically Assess a Placer Gold Deposit’s Value? (Key to Avoiding Blind Investment!)
Scientific assessment involves systematic exploration (pitting, trenching, drilling) and, crucially, representative bulk sampling to determine average grade, gold particle size, and material characteristics like clay content and washability.
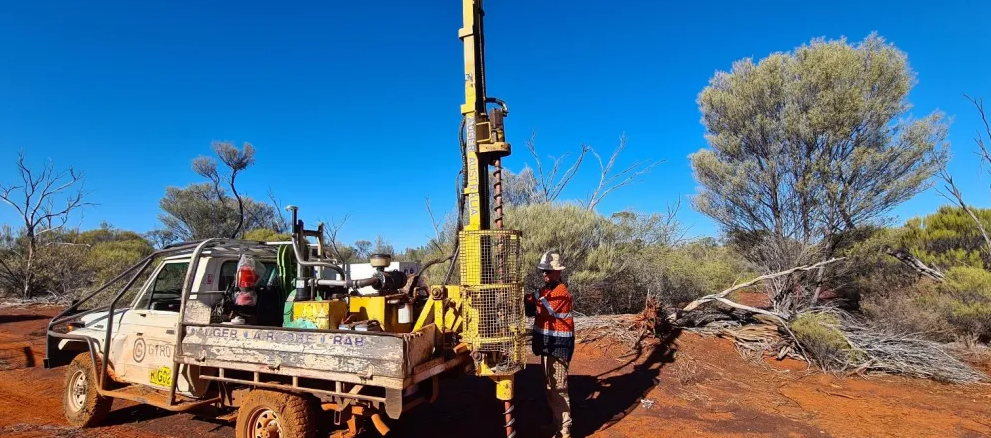
Deeper Dive: From Prospecting to Resource Definition
Making informed investment decisions requires moving beyond basic prospecting:
Exploration Techniques
Common methods to understand the deposit’s extent and characteristics include:
- Geophysical Surveys (Less Common): Methods like ground-penetrating radar (GPR) or resistivity can sometimes help map bedrock topography or buried channels, but direct sampling is usually needed.
- Pitting and Trenching: Digging pits or trenches down to bedrock (or the base of the pay layer) allows visual inspection of the gravel layers and collection of samples across the vertical profile. Best for shallow deposits.
- Drilling: Using auger drills or larger diameter reverse circulation (RC) or sonic drills allows sampling deeper deposits or covering larger areas more quickly than pitting. Accurate sample collection is critical.
The Crucial Role of Bulk Sampling (Insight!)
- Why Panning Isn’t Enough: Insight: Pan samples are notoriously unreliable for grade estimation. Placer gold distribution is often erratic (the “nugget effect”). A few good pans don’t represent the whole deposit. Relying only on pan samples is a major reason why operations fail.
- The Need for Volume: To get a statistically reliable average grade (e.g., grams per cubic meter or ounces per cubic yard), you must process significant volumes (several cubic meters/yards) from various representative locations across the deposit.
- Pilot Testing: This bulk sampling is often done using a small-scale test plant (like a highbanker or small trommel) to simulate the actual recovery process.
Key Data Points from Sampling
- Gold Grade: The average amount of recoverable gold per unit volume or weight.
- Gold Particle Size Distribution: Are you dealing with coarse nuggets, flakes, or mostly fine/microscopic gold? Insight: This heavily influences the choice of recovery equipment (sluices vs. jigs vs. centrifuges). Fine gold recovery is often key to profitability.
- Pay Gravel Thickness & Depth: How much material needs to be moved to access the gold-bearing layer?
- Clay Content & Washability: Insight: Clay is often the enemy of recovery. High clay content requires aggressive scrubbing and can carry away fine gold if not properly handled. Test how easily the material breaks down in water.
- Gravel Size / Boulders: Presence of large boulders impacts excavation and screen size selection.
What is the Core Process Flow for Commercial Placer Gold Mining?
The core process involves: Excavation (digging the pay gravel), Feeding/Screening (removing oversized rocks, initial washing), Scrubbing/Washing (breaking down clays), Concentration (using gravity methods like sluices, jigs, centrifuges), and Refining/Tailings Management.
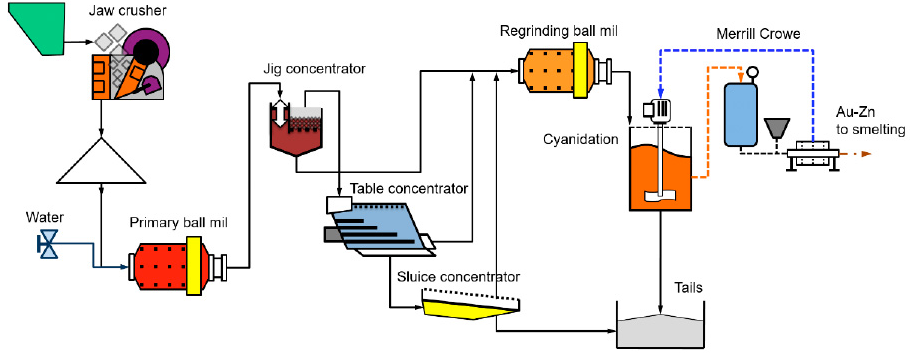
From Pit to Product
A typical commercial placer operation follows these steps:
Excavation & Transport
- Goal: Dig the gold-bearing gravel (“paydirt”) and transport it to the processing plant.
- Equipment: Excavators, bulldozers (for stripping overburden), front-end loaders, dump trucks, or sometimes dredges (for underwater deposits). Insight: The excavation rate must be balanced with the plant’s processing capacity.
Feeding & Screening
- Goal: Feed the plant consistently and remove large, barren rocks (oversize) that don’t need further processing. Initial washing often starts here.
- Equipment: Feed Hoppers with Grizzly bars (to reject very large rocks), Vibrating Screens or Rotary Trommel Screens (to wash and size the material). Insight: Choosing between vibrating screens and trommels depends on material characteristics, especially clay content and desired scrubbing action. ZONEDING offers both types.
Washing & Scrubbing (Clay Management – Insight!)
- Goal: Break down any clay lumps or cemented gravels to liberate trapped gold particles.
- Equipment: Insight: This step is critical if clay is present. Trommels often have integrated scrubber sections with lifter bars. Log Washers or dedicated Rotary Scrubbers provide more aggressive action for very clay-rich ores. High-pressure water sprays on screens also help. Inadequate scrubbing leads to major gold losses.
Concentration (Primary Recovery)
- Goal: Separate the heavy gold particles from the bulk of the lighter sand and gravel using gravity.
- Equipment: This is the heart of the plant. Common choices include:
- Sluice Boxes: Simple, inclined troughs with riffles (barriers) to trap gold. Various types exist (e.g., standard, pulsating, vibrating). Efficient for coarser gold but less so for fines.
- Jigs: Use pulsed water flow through a screen bed to stratify material by density, concentrating heavy minerals (including gold). Effective for specific size ranges.
- Centrifugal Concentrators (e.g., Knelson, Falcon types): Use high G-forces to separate fine and even microscopic gold particles very efficiently. Insight: Often essential for maximizing recovery, especially where fine gold dominates. ZONEDING supplies high-efficiency gravity concentration equipment.
Fine Gold Recovery & Upgrading (Insight!)
- Goal: Further concentrate the product from the primary recovery stage and capture very fine gold.
- Equipment: Concentrates from sluices/jigs/centrifuges are often further upgraded using:
- Shaking Tables: Use vibration and water flow across a riffled deck to separate gold from other heavy minerals.
- Smaller Centrifuges or Spiral Concentrators.
- Insight: This “clean-up” circuit is where the final high-grade gold concentrate is produced before smelting.
Tailings & Water Management
- Goal: Manage the waste material (tailings) and recycle process water.
- Equipment: Settling Ponds (to clarify water), potentially thickeners or filters, pumps and pipelines for water recirculation. Insight: Effective water management is crucial for consistent operation and environmental compliance.
How to Select the Right Placer Gold Equipment for Maximum Recovery (Especially Fine Gold)?
Choosing the wrong equipment means lost gold and wasted money. How do you pick the best screens, concentrators, and washers for your specific deposit?
Selection depends on throughput needs, feed size, clay content, and crucially, the gold particle size distribution. For fine gold, efficient screening and specialized recovery units like centrifugal concentrators are vital alongside traditional methods.
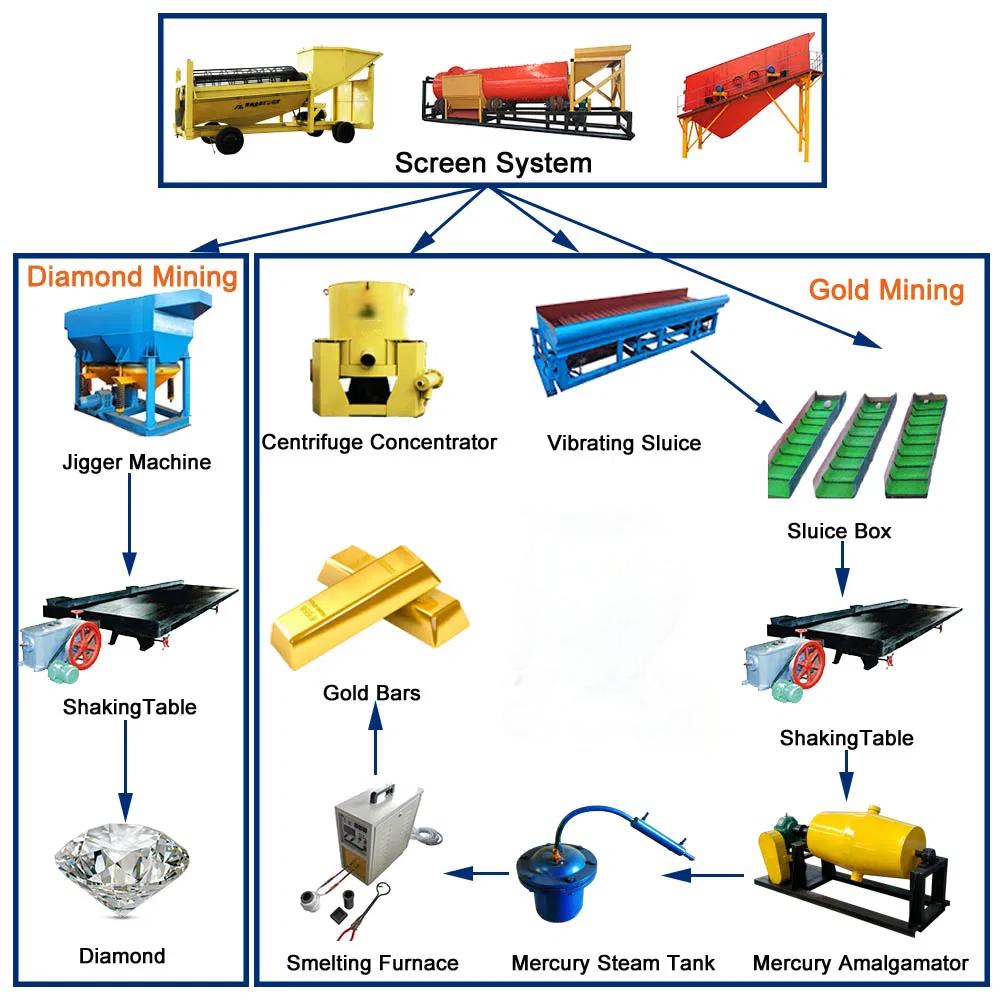
Matching Machines to Material
Making the right equipment choices requires understanding their strengths and weaknesses:
Screening: Trommel vs. Vibrating Screen
- Rotary Trommel Screens: Excellent for washing and scrubbing clay-rich material due to tumbling action and longer retention time. Often include a scrubber section. Good for handling variable feed. ZONEDING trommels are robustly built.
- Vibrating Screens: High screening efficiency for specific size cuts, better for handling high volumes of free-flowing material with less clay. Often use high-pressure spray bars for washing.
- Selection: Choose based on clay content (trommel preferred for high clay), required throughput, and desired product size fractions. Screen opening size is critical – it determines the maximum particle size reporting to the recovery circuit.
Primary Concentration: Sluices, Jigs, Centrifuges
- Sluice Boxes: Simple, relatively low cost. Best suited for recovering coarser gold (>1mm). Efficiency drops rapidly for fine gold. Requires careful water flow and feed rate control. Different riffle types and matting (e.g., vortex) can improve fine gold capture somewhat.
- Jigs: Effective for recovering gold in a specific size range (e.g., 1mm to 10mm). Less sensitive to feed fluctuations than sluices. Requires consistent water pulsation.
- Centrifugal Concentrators: Insight: The industry standard for recovering fine (-1mm) and even microscopic gold. Generate high G-forces for efficient separation. Crucial for deposits where most value is in fines. Available in batch or semi-continuous discharge types. ZONEDING offers reliable centrifugal concentrators.
Handling Clay: Scrubbers & Log Washers
- Rotary Scrubbers / Trommel Scrubber Sections: Use lifter bars and water to tumble and break down clay lumps as material passes through. Integral to many trommel designs.
- Log Washers: More aggressive scrubbing action using rotating paddles on shafts. Used for very heavy, sticky clays that trommels struggle with.
Equipment Sizing
- All equipment must be sized appropriately for the target throughput (cubic meters or tonnes per hour). Undersized equipment creates bottlenecks and reduces efficiency. Oversized equipment increases capital cost unnecessarily.
Mobile Gold Plant vs. Fixed Plant: How Should I Choose?
Debating whether a portable wash plant or a permanent, stationary setup is right for you? This choice significantly impacts flexibility, cost, and processing capacity.
Mobile plants offer flexibility and fast deployment for smaller or shorter-term deposits. Fixed plants provide higher throughput, stability, and process optimization potential but require larger investment and longer setup times.
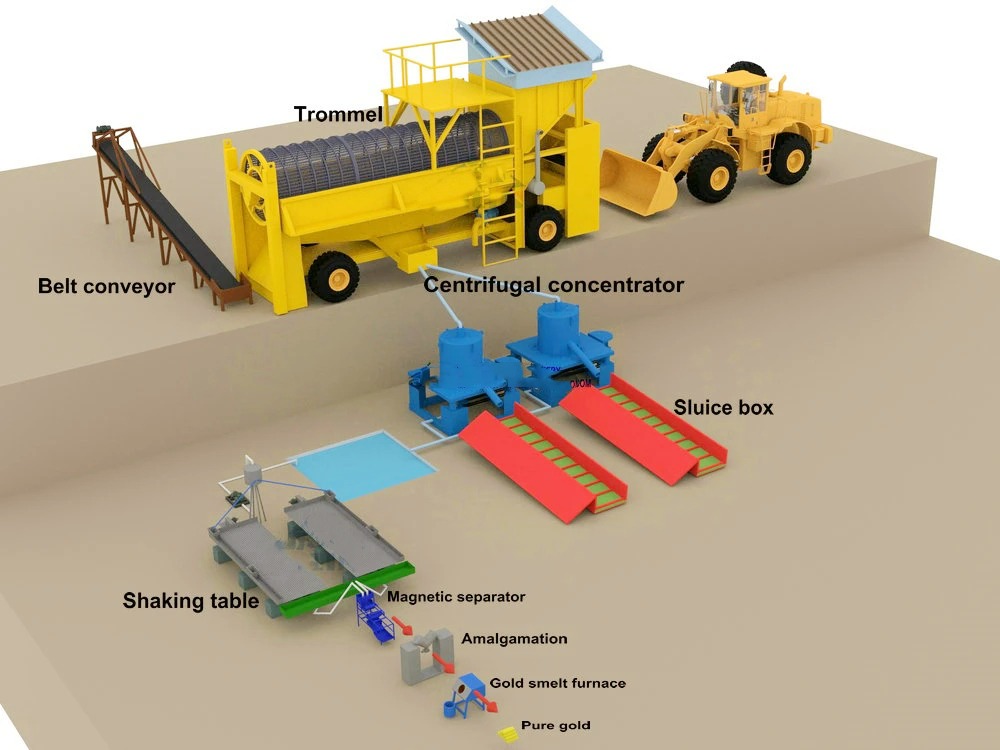
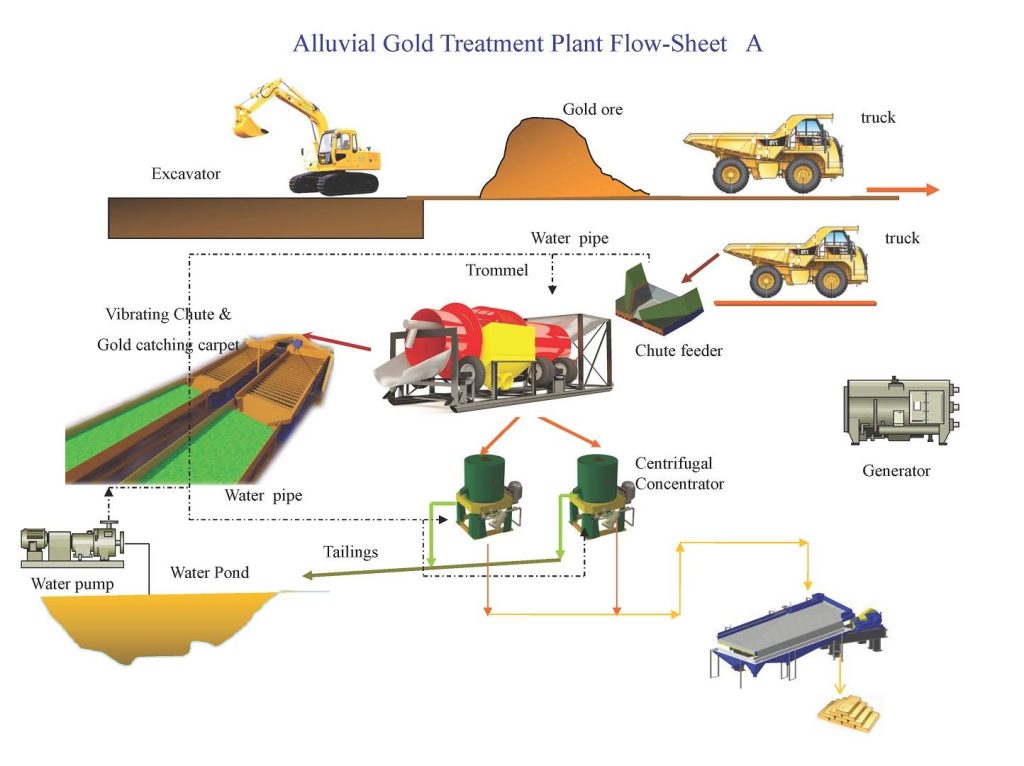
Portability vs. Permanence
The decision depends heavily on your project specifics:
Mobile Gold Plants
- Design: Typically integrates screening, washing, and primary recovery (often sluices, sometimes small jigs or centrifuges) onto a single wheeled or skid-mounted chassis.
- Advantages:
- Flexibility: Easily moved between different mining areas or deposits.
- Rapid Deployment: Minimal site preparation needed, faster start-up.
- Lower Initial CAPEX: Generally less expensive than building a fixed plant of similar small capacity.
- Good for exploration bulk sampling or very small operations.
- Disadvantages:
- Limited Throughput: Processing capacity is usually much lower than fixed plants.
- Process Limitations: Often simpler circuits, potentially lower recovery (especially for fine gold) compared to optimized fixed plants.
- Stability Issues: Can be less stable during operation, potentially affecting recovery efficiency.
- Wear and tear can be higher due to lighter construction.
Fixed (Stationary) Placer Plants
- Design: Components (screens, scrubbers, concentrators, pumps) are installed on concrete foundations or robust steel structures. Allows for more complex and optimized circuit design.
- Advantages:
- Higher Throughput: Can be designed for much larger processing capacities.
- Optimized Recovery: Allows for better process control, more stages of concentration, and dedicated fine gold recovery circuits. Typically achieves higher overall recovery.
- Stability & Durability: More stable operation, often uses heavier-duty equipment designed for longer life.
- Disadvantages:
- Higher Initial CAPEX: Significant investment in equipment, civil works, and installation.
- Longer Construction Time: Takes longer to design, permit, build, and commission.
- Immobility: Cannot be easily relocated.
Decision Factors
- Deposit Size & Mine Life: Large, long-life deposits justify fixed plants. Small, scattered, or short-life deposits favor mobile units.
- Throughput Requirement: High tonnage demands a fixed plant.
- Terrain & Access: Difficult terrain might favor mobile plants.
- Investment Budget: CAPEX limitations might dictate starting with a mobile unit.
- Operational Strategy: Exploration vs. full-scale production.
How to Configure a Complete Placer Plant Based on Throughput (m³/hour)?
Planning your production line but unsure how to match equipment capacities? Sizing and linking the different processing stages correctly is essential for efficient operation.
Start with the target throughput (e.g., 100 cubic meters/hour). Select primary equipment (screen, scrubber, primary concentrators) capable of handling slightly more than this rate. Ensure downstream equipment (pumps, fine recovery, conveyors) can handle the expected concentrate/tailings flows.
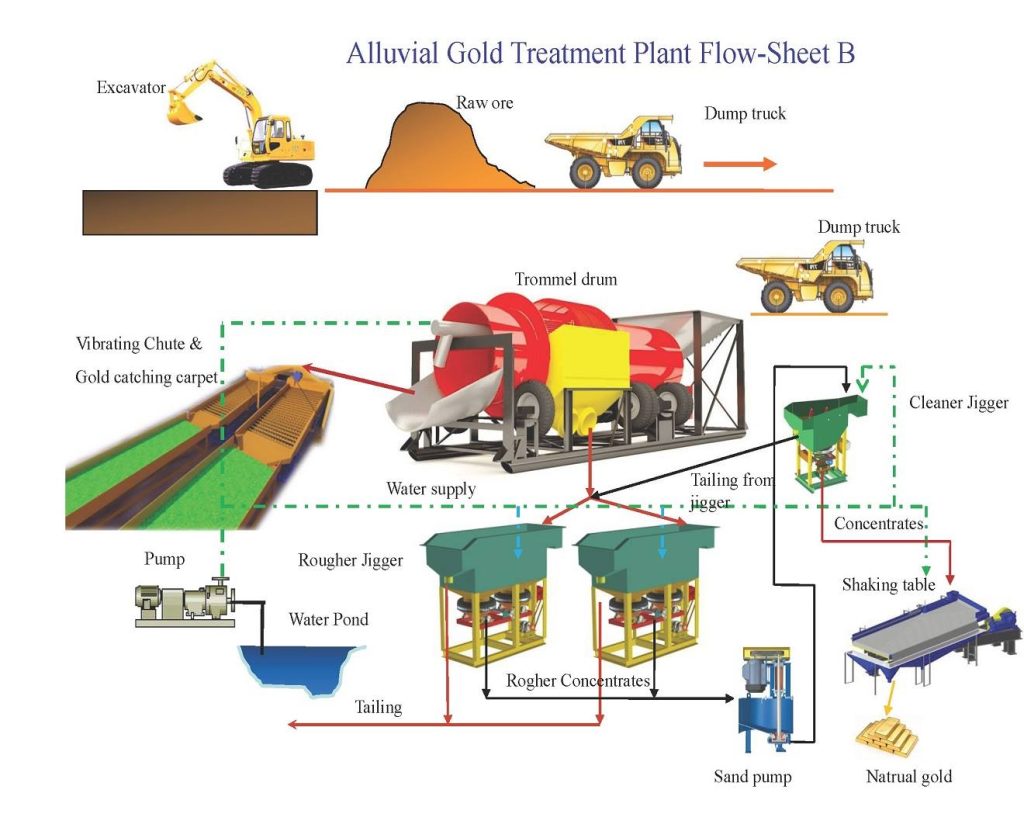
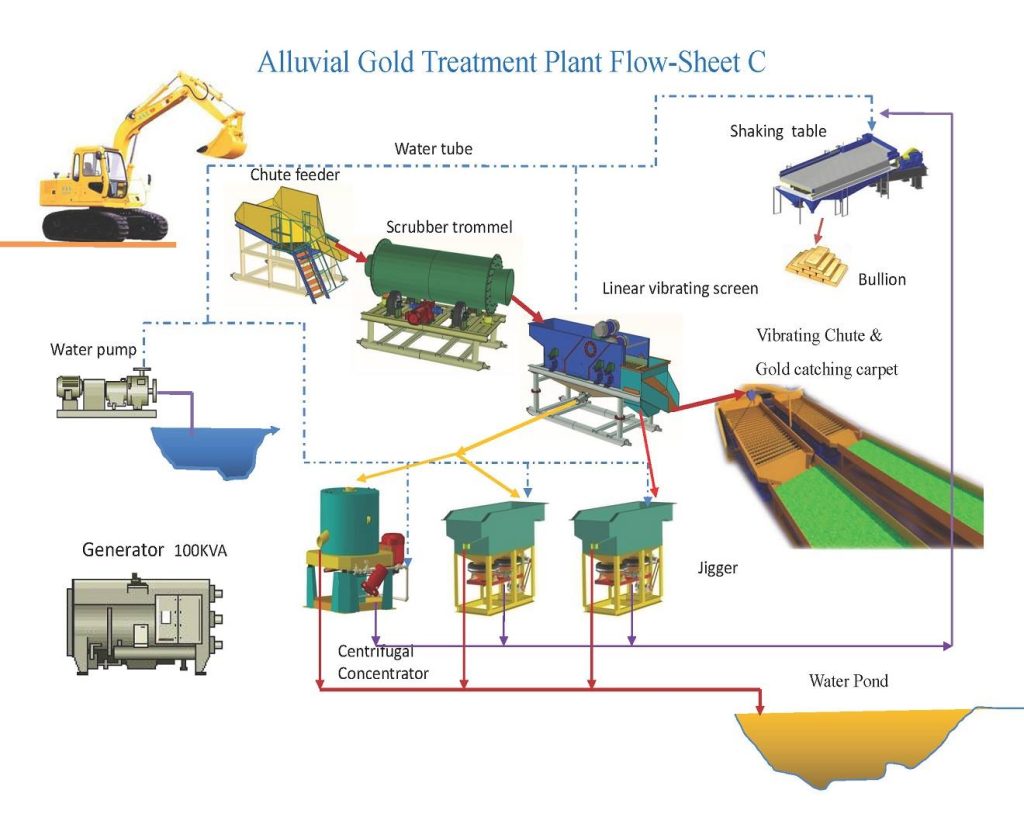
Balancing the Line
Configuring the plant involves matching capacities and ensuring smooth flow:
Estimating Throughput Needs
- Based on the deposit size, grade, desired production rate, and mine life. Expressed typically in cubic meters or tonnes per hour of feed material.
Matching Primary Equipment
- Feed Hopper/System: Must handle the excavator/loader bucket size and provide a reasonably consistent feed rate to the screen.
- Screen/Trommel: Select a model rated for slightly above your target throughput (e.g., if targeting 100 m³/hr, choose a screen rated for 110-120 m³/hr) to handle surges and ensure effective washing/screening. Consider the percentage of oversize expected.
- Scrubber (if needed): Must provide adequate retention time at the target feed rate to break down clays.
- Primary Concentrators (Sluices/Jigs/Centrifuges): Size based on the flow rate of the undersize material coming from the screen. Ensure sufficient capacity to handle the design flow without overloading, which drastically reduces recovery.
Connecting the Units
- Material Transport: Use appropriately sized Conveyors or slurry Pipelines to move material between stages (e.g., screen undersize to concentrators, concentrates to clean-up, tailings to disposal).
- Slurry Pumps: Size pumps based on required flow rate, slurry density, and the vertical/horizontal distance (head) they need to pump. Factor in friction losses. ZONEDING offers robust slurry pumps.
Water Balance & Auxiliary Needs
- Calculate the total process water required for screening, scrubbing, sluicing, jigging, etc.
- Size Water Pumps and Pipelines accordingly.
- Include Settling Ponds and recycle pumps if implementing water recirculation.
- Consider the need for concentrate handling systems (secure containers, pumps).
Bottleneck Management (Insight!)
- Insight: Identify the potential bottlenecks. Is it the excavator’s digging rate? The screen’s capacity? The water supply? The entire line is only as fast as its slowest component. Ensure a balanced design where no single stage severely limits overall throughput.
Water and Power: Lifelines for Placer Mining – How to Plan and Manage?
Recognizing that water and power are essential, but facing challenges like remote locations or water scarcity? Proper planning for these utilities is non-negotiable.
Assess water needs based on plant design (often 2-5 cubic meters of water per cubic meter of processed solids). Plan for sourcing, pumping, and efficient recycling via settling ponds. Choose power source (grid vs. diesel generator) based on availability, cost, and total plant load.
Deeper Dive: Utility Planning
Operations stop without reliable water and power:
Water Management Strategy
- Estimating Needs: Calculate water requirements for each stage (washing, slurry transport, concentration). Typically ranges from 2:1 to 5:1 water-to-solids ratio by volume, but varies with equipment and ore type.
- Sourcing: Identify reliable sources: rivers, streams, boreholes, existing ponds. Secure necessary water use permits.
- Water Scarcity Solutions:
- Efficient Recycling: Design large, effective Settling Ponds to allow solids (slimes) to settle out so water can be reused. Insight: Dirty recycle water with high solids increases slurry viscosity and hurts fine gold recovery. Multiple ponds in series work best. Consider using flocculants to speed settling if needed.
- Minimize losses through leaks and evaporation.
- Pumping & Distribution: Select appropriate pumps and pipelines to deliver water where needed at the right pressure and volume.
Power Supply Planning
- Estimate Load: Calculate the total power consumption of all electric motors (screens, pumps, conveyors, centrifuges, jigs, lights, camp). Sum the kilowatts (kW).
- Source Options:
- Grid Power: Ideal if available and reliable – usually the cheapest option. Requires connection infrastructure (transformers, power lines).
- Diesel Generators: Common for remote sites. Must be sized correctly (typically 1.25x to 1.5x the total running load to handle motor starting currents). Requires reliable fuel supply and maintenance. Calculate fuel consumption for cost estimation.
- Distribution: Proper electrical switchgear, motor control centers (MCCs), and site cabling are essential for safety and reliability.
What are the Main Operating Costs in a Commercial Placer Gold Project? How to Control Them?
Moving beyond initial investment, what ongoing costs will determine your profitability? Understanding and managing OPEX is crucial for survival.
Major operating costs include fuel/electricity (for excavation and processing), equipment maintenance and wear parts, labor, water management (if pumping/treating), and environmental compliance/reclamation.
Deeper Dive: Keeping Costs in Check
Profitability depends on keeping OPEX under control:
Key Cost Centers
- Fuel/Electricity: Often the largest single operating cost, especially if relying on diesel generators. Powering excavators, loaders, pumps, screens, etc.
- Maintenance & Wear Parts: Insight: Processing abrasive gravel causes significant wear. Budget for regular replacement of screen decks, trommel shells/lifters, pump impellers/liners, sluice riffles/matting, conveyor belts, cutting edges/teeth for excavators. Preventative maintenance reduces costly breakdowns. Reliable equipment from suppliers like ZONEDING minimizes unexpected failures.
- Labor: Salaries and wages for operators, maintenance crew, supervisors, security, camp staff.
- Water Management: Costs associated with pumping fresh water, operating recycle systems, potentially purchasing water, or treating discharge water.
- Environmental & Reclamation: Costs for monitoring, implementing erosion controls, progressive reclamation activities, and final site closure bonding.
- Supplies: Lubricants, welding consumables, miscellaneous camp supplies.
- Transportation: Costs for moving fuel, parts, supplies, and personnel to site.
Cost Control Strategies
- Optimize Fuel Efficiency: Use appropriately sized equipment, maintain engines well, minimize idling time. Grid power is usually cheaper if accessible.
- Manage Wear: Use high-quality wear parts. Implement hard-facing on high-wear areas. Proper lubrication reduces friction and wear.
- Efficient Water Recycling: Reduces the need for fresh water pumping.
- Preventative Maintenance: Scheduled maintenance is cheaper than emergency repairs and extended downtime.
- Process Optimization: Ensure the plant is running efficiently (correct water flows, feed rates) to maximize gold recovery per tonne processed. Minimize gold losses to tailings.
- Effective Mine Planning: Minimize haul distances and material re-handling.
What are the Environmental Impacts and Compliance Requirements for Placer Mining?
Operating responsibly means understanding and managing your environmental footprint. What are the key regulations and concerns?
Key issues include water quality (sediment discharge), erosion control, habitat disturbance, and land reclamation. Compliance requires obtaining permits, implementing mitigation measures, and adhering to discharge standards and reclamation plans.
Deeper Dive: Operating Sustainably
Environmental regulations are becoming increasingly stringent globally:
Major Environmental Considerations
- Water Quality: Discharge of muddy water (high suspended solids) into rivers is often strictly regulated. Settling ponds are essential to clarify process water before discharge or recycling. Accidental spills of fuel/lubricants must be prevented and managed.
- Erosion & Sediment Control: Stripping vegetation and excavating large areas increases erosion risk. Measures like silt fences, check dams, and diversion ditches may be required.
- Habitat Disturbance: Mining activities impact local ecosystems. Minimizing the footprint and avoiding sensitive areas is important.
- Land Reclamation: Insight: Plan for reclamation from the start. Most jurisdictions require mined land to be reshaped, topsoiled (if saved), and revegetated to a stable and productive state. Progressive reclamation (reclaiming areas as they are finished) is often preferred and can reduce bonding costs.
Permitting & Compliance
- Licenses & Permits: Operations typically require multiple permits, potentially including:
- Mining Lease/Claim License
- Environmental Permits (covering water discharge, land disturbance, air quality if applicable)
- Water Use Permits
- Land Use Permits
- Compliance Monitoring: Regulators often require regular monitoring of water quality, erosion controls, and reclamation progress.
How to Choose a Reliable Placer Gold Equipment Supplier or Plant Provider?
Ready to purchase equipment or commission a full plant? Selecting the right partner is crucial for getting reliable machinery and effective solutions.
Evaluate suppliers on their proven experience in placer gold projects, technical expertise (including testing/design), equipment quality and robustness, availability of support and spare parts, and transparency in pricing and specifications.
Efficient placer gold mining requires more than just moving dirt. Success demands careful deposit evaluation, smart flowsheet design tailored to the ore (especially regarding clay and fine gold), selecting robust and appropriate equipment, diligent operational management (costs, water, power), and responsible environmental practices. ZONEDING MACHINE offers reliable equipment and expertise to support your placer gold venture.