Nickel Ore Beneficiation Plant Solutions
Nickel ores consist primarily of copper-nickel sulfide ore and nickel oxide ore, specifically laterite nickel ore. The primary method for beneficiation of nickel ore is the flotation process, with magnetic separation and gravity separation often serving as supplementary beneficiation methods.
To fully exploit resources and maximize economic benefits, the nickel ore beneficiation process and equipment can be customized accordingly.
Please note that the specific beneficiation process and equipment may be tailored to suit individual requirements, ensuring the comprehensive utilization of resources and the attainment of optimal economic outcomes.
How to Choose the Right Technology for Nickel Ore Beneficiation: Sulfide Flotation vs. Laterite Upgrading?
Choosing the right path hinges on ore type. Sulfide nickel ores are primarily processed using froth flotation to produce concentrates. Laterite nickel ores generally require hydrometallurgical (leaching) or pyrometallurgical (smelting) methods, often after some physical pre-treatment.
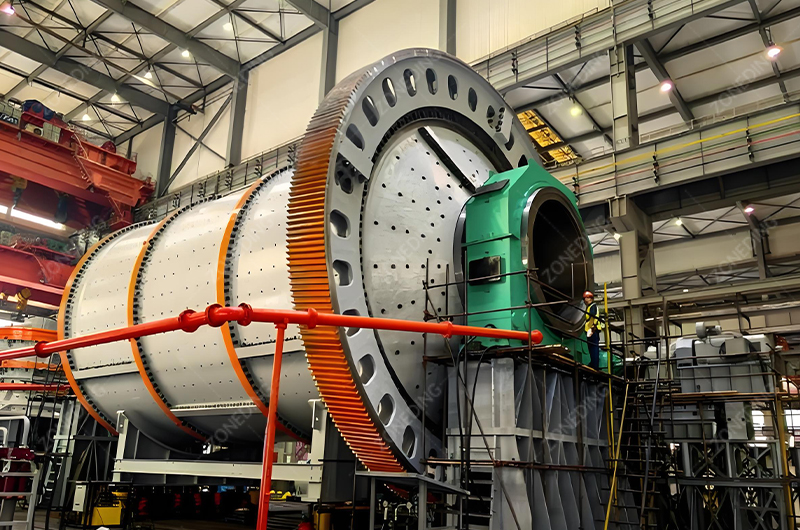
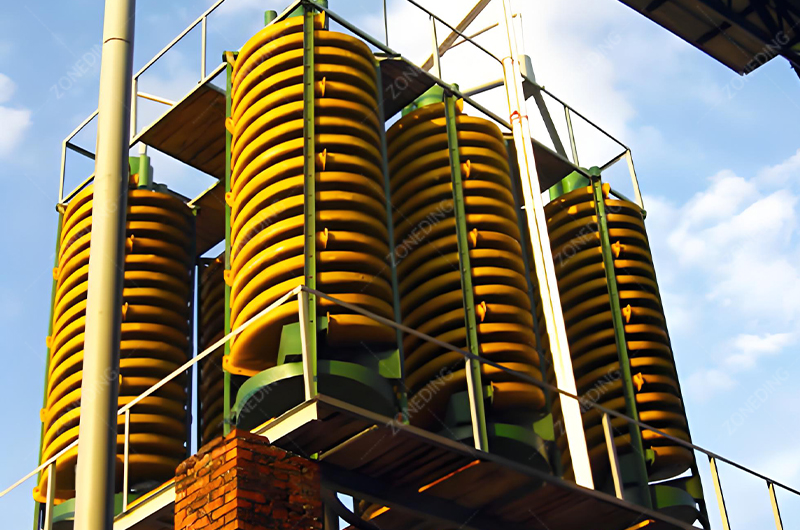
The journey from nickel ore to a valuable product follows dramatically different paths depending on its geological origin. Understanding these differences is the absolute first step toward a successful operation.
Is The Nickel Ore Sulfide or Laterite? Why Must This Be Clarified First?
Identifying the ore type (sulfide vs. laterite) is paramount because they require fundamentally different processing technologies. Sulfides are amenable to physical concentration (flotation), while laterites need chemical processing (leaching or smelting). Applying the wrong method guarantees failure.
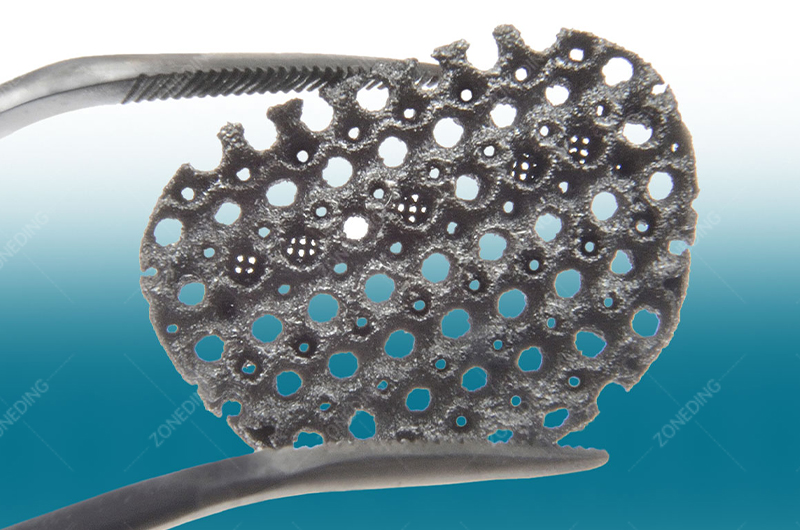

The Great Divide: Sulfide vs. Laterite
Confusing these two ore types is the most common and dangerous mistake in nickel processing. Their origins and mineralogy dictate entirely separate approaches.
- Sulfide Nickel Ores:
- Minerals: Nickel primarily occurs in sulfide minerals like Pentlandite ((Fe,Ni)₉S₈), often associated with chalcopyrite (CuFeS₂), pyrrhotite (Fe₁₋ₓS), pyrite (FeS₂), and Platinum Group Metals (PGMs).
- Processing Goal: Concentrate the valuable sulfide minerals away from waste rock (gangue) using physical methods, primarily froth flotation, to produce a high-grade nickel concentrate (often containing Cu, Co, PGMs) suitable for smelting.
- Laterite Nickel Ores:
- Minerals: Formed by intense weathering in tropical climates. Nickel does not occur as distinct sulfide minerals. Instead, it’s chemically incorporated into the crystal lattices of:
- Silicate minerals: Like serpentine or garnierite in the lower Saprolite layer.
- Iron/Manganese oxy-hydroxides: Like goethite in the upper Limonite layer.
- Processing Goal: Extract nickel using chemical methods because physical separation is ineffective. Main routes are Hydrometallurgy (e.g., High-Pressure Acid Leaching – HPAL) or Pyrometallurgy (e.g., Rotary Kiln-Electric Furnace – RKEF smelting to produce Ferronickel). Physical “beneficiation” is usually limited to simple washing and screening for upgrading or preparation.
- Minerals: Formed by intense weathering in tropical climates. Nickel does not occur as distinct sulfide minerals. Instead, it’s chemically incorporated into the crystal lattices of:
Mixing these up is disastrous. Applying flotation to laterites won’t work. Trying to directly smelt low-grade sulfide ore is uneconomic. Accurate mineralogical identification is non-negotiable before designing any plant. ZONEDING provides robust initial Crushing Equipment and grinding mills (Ball Mill) suitable for preparing either ore type for its correct downstream process.
For Sulfide Nickel Ore: How Did Flotation Become the Main Method?
Froth flotation became the standard for sulfide nickel because it effectively separates fine nickel sulfide minerals (like pentlandite) from non-sulfide gangue based on surface chemical properties. This allows the production of high-grade concentrates suitable for smelting, which other methods typically cannot achieve efficiently.
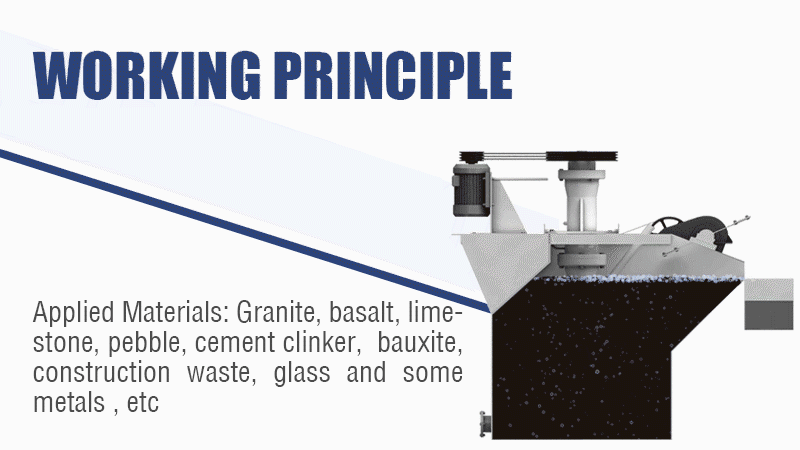
The Power of Surface Chemistry
Flotation technology revolutionized the processing of many sulfide ores, including nickel.
- The Challenge: Nickel sulfide minerals like pentlandite are often finely disseminated within the host rock and mixed with other sulfides (copper, iron) and silicate gangue. Simple gravity separation is usually ineffective due to insufficient density differences, especially at fine sizes. While some associated minerals like pyrrhotite are magnetic, pentlandite itself is not, limiting the primary use of magnetic separation.
- Flotation Principle: Flotation exploits differences in the surface chemistry of minerals. Specific chemicals (collectors) are added to the ore slurry (Mixer tanks) that selectively adsorb onto the surface of sulfide minerals, making them hydrophobic (water-repellent). When air is bubbled through the slurry in Flotation Machines, these hydrophobic particles attach to the air bubbles and rise to the surface, forming a froth that can be collected. Gangue minerals remain hydrophilic (water-loving) and stay in the pulp.
- Effectiveness: This allows for efficient concentration of even very fine sulfide particles, achieving high recovery rates and producing a significantly upgraded concentrate essential for economic smelting.
Flotation’s ability to selectively recover fine, disseminated sulfide minerals based on surface properties makes it the indispensable core technology for treating sulfide nickel ores globally.
How Should Crushing and Grinding Prepare Sulfide Nickel for Efficient Flotation? (Particle Size & Liberation)
Crushing (Jaw Crusher, Cone Crusher) and grinding (Ball Mill) reduce the ore size to liberate the nickel sulfide particles from the surrounding gangue matrix. The target grind size aims to maximize liberation while avoiding excessive over-grinding, which wastes energy and can hinder flotation.
Setting the Stage for Separation: Liberation
Proper size reduction (comminution) is critical for successful flotation.
- The Goal: Liberation: The primary objective is to break the ore down so that individual nickel sulfide particles are substantially free (“liberated”) from adhering gangue minerals. If particles remain locked (nickel sulfide still attached to gangue), flotation cannot effectively separate them.
- Determining Grind Size: The required fineness depends on the natural grain size and texture of the nickel minerals within the specific ore deposit. This is determined through mineralogical analysis (microscopy). Grinding must be sufficient to achieve adequate liberation.
- Comminution Circuit: Typically involves multiple stages:
- Crushing: Coarse reduction using Jaw Crushers followed by secondary/tertiary Cone Crushers or Impact Crushers.
- Grinding: Finer reduction, usually in rotating mills like Ball Mills or semi-autogenous (SAG)/autogenous (AG) mills, often operating in closed circuit with classifiers (Hydrocyclone or Vibrating Screen) to ensure particles reach the target size.
- Avoiding Over-Grinding: While liberation is essential, grinding too fine (over-grinding) is detrimental. It consumes excessive energy, can generate ultra-fine “slimes” that are difficult to float efficiently, may increase reagent consumption, and can sometimes worsen selectivity. Achieving the optimal balance is key.
ZONEDING provides reliable and efficient crushing, grinding, and screening solutions designed to achieve the necessary liberation for effective downstream flotation.
Keys to Sulfide Nickel Flotation: How to Select Suitable Reagents and Optimize the Flowsheet?
Optimizing sulfide nickel flotation requires selecting appropriate collectors (often xanthates) and frothers (e.g., MIBC). Crucially, it involves precise control of pH (using lime/soda) and specific modifiers to depress unwanted pyrrhotite and selectively separate copper minerals.
Mastering the Chemistry: Reagents and Control
Achieving good recovery and concentrate quality in nickel flotation is a balancing act controlled by chemistry.
- Reagent Suite:
- Collectors: Chemicals that adsorb onto nickel sulfide surfaces, making them hydrophobic. Short-chain Xanthates (e.g., PAX, SIBX) are commonly used.
- Frothers: Chemicals that stabilize air bubbles, creating a manageable froth layer. Alcohols like MIBC (Methyl Isobutyl Carbinol) or glycol ethers are common.
- Activators: Sometimes used to enhance collector adsorption (e.g., copper sulfate can activate some nickel minerals, but must be used carefully if copper separation is needed).
- pH Modifiers: Lime (CaO) or Soda Ash (Na₂CO₃) are critical for raising pulp pH. High pH (typically 9-11) is essential for depressing naturally floatable iron sulfides, particularly pyrrhotite and pyrite.
- Depressants: Chemicals used to prevent specific minerals from floating. Besides pH control, other depressants might include sulfites, SO₂, or (used sparingly and carefully due to toxicity) cyanide, particularly for enhancing copper-nickel separation or depressing pyrite/arsenopyrite.
- Flowsheet Optimization:
- Pyrrhotite Rejection: The primary challenge is often rejecting pyrrhotite, which floats readily with pentlandite but dilutes the concentrate. High pH is the main tool.
- Copper-Nickel Separation: If significant copper (chalcopyrite) is present, specialized flotation schemes are needed (see next section).
- Circuit Design: May involve rougher, scavenger, and multiple cleaner stages in Flotation Machines to maximize recovery and achieve target concentrate grade. Conditioning tanks (Mixer tanks) ensure proper reagent mixing.
Reagent selection and circuit design are highly ore-specific. Extensive laboratory test work and pilot plant trials are necessary to determine the optimal conditions for any given sulfide nickel deposit.
How to Effectively Separate Commonly Associated Copper Minerals in Sulfide Nickel Ore? (Copper-Nickel Separation)
Copper-nickel separation relies on exploiting subtle differences in their flotation behavior using carefully controlled chemistry. Typically, high pH (lime) is used to depress nickel and iron sulfides more than copper sulfides, allowing selective flotation of copper first.
The Art of Selective Flotation
Separating chalcopyrite (CuFeS₂) from pentlandite ((Fe,Ni)₉S₈) is a classic challenge in sulfide mineral processing.
- The Problem: Both minerals respond well to similar collectors under standard conditions, making separation difficult.
- Common Strategies:
- Sequential Flotation (Cu first, then Ni): This is the most common approach.
- Copper Stage: Operate the initial flotation stage at high pH (e.g., pH 10-12 using lime). Lime strongly depresses pentlandite and iron sulfides (pyrite, pyrrhotite) but affects chalcopyrite less. Using a suitable collector, chalcopyrite floats preferentially into a copper concentrate.
- Nickel Stage: The tailings from the copper circuit (containing the depressed nickel) are then conditioned, often by lowering the pH slightly and/or adding an activator (like copper sulfate, carefully controlled) to reactivate the pentlandite. A nickel collector is added, and pentlandite is floated into a separate nickel concentrate.
- Bulk Flotation then Separation: Float both copper and nickel together in a bulk concentrate first. Then, subject this bulk concentrate to a secondary flotation step where conditions are adjusted (e.g., adding SO₂ or other depressants) to depress one mineral while floating the other. This is less common for primary Cu-Ni separation but sometimes used.
- Sequential Flotation (Cu first, then Ni): This is the most common approach.
- Key Control Factor: Precise pH control with lime is the cornerstone of most Cu-Ni separation circuits (Insight #2). Other depressants (like small, controlled amounts of cyanide or specific organic reagents) might be used to further enhance selectivity, but their use requires careful testing and management.
Achieving efficient Cu-Ni separation requires experienced metallurgical oversight, rigorous process control, and optimization based on the specific ore characteristics. It’s often the most complex part of a sulfide nickel flotation plant.
Pyrrhotite and Other Iron Sulfides: Friend or Foe in Sulfide Nickel Processing? (Magnetic Separation/Depression)
Pyrrhotite and pyrite are generally foes in nickel flotation. They dilute concentrate grade, add excess sulfur (problematic for smelting), and consume reagents. They are primarily managed via chemical depression (high pH) during flotation, with magnetic separation sometimes used to remove pyrrhotite.
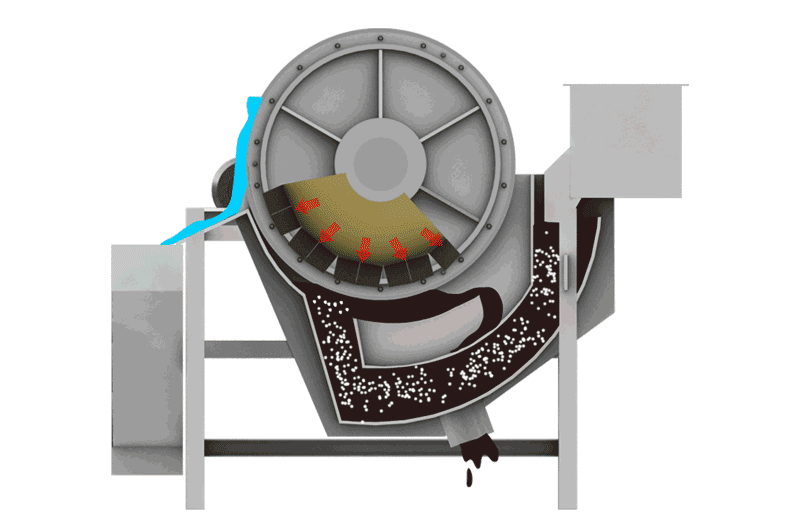
Managing Iron Sulfides
Controlling iron sulfides is essential for producing a marketable nickel concentrate.
- Why They Are Problematic:
- Dilution: They contain little or no nickel but often float readily with pentlandite, lowering the final nickel concentrate grade.
- Smelting Issues: They contribute significant sulfur to the concentrate. Smelters often have strict limits on the Ni/S ratio or total sulfur load, as excess sulfur requires extra processing steps and can cause environmental issues (SO₂ emissions).
- Reagent Consumption: They consume flotation reagents, increasing operating costs.
- Management Strategies:
- Chemical Depression (Primary Method): As discussed, maintaining a high pulp pH (9-11 or higher) using lime or soda ash is the main technique to depress the flotation of both pyrrhotite and pyrite while allowing pentlandite (and chalcopyrite) to float.
- Magnetic Separation: Pyrrhotite is unique among common sulfides in being noticeably magnetic (varying from weakly to strongly magnetic depending on its exact composition). This property allows it to be removed using Magnetic Separators. This can be done:
- Before flotation: To remove bulk magnetic pyrrhotite from the feed, reducing the load on the flotation circuit.
- After flotation: To clean pyrrhotite from either the final concentrate or tailings streams.
- Note: Some nickel can be locked within the pyrrhotite structure, so magnetic removal might lead to some nickel loss, requiring careful evaluation.
- Potential “Friend”? In rare cases, pyrrhotite might contain recoverable amounts of cobalt or PGMs, slightly complicating its status. However, in most nickel operations, its negative impacts heavily outweigh any potential benefit, and rejection is the goal.
Effective rejection of iron sulfides, primarily through pH control during flotation and potentially augmented by magnetic separation, is crucial for achieving target nickel concentrate quality.
How Do Troublesome Gangue Minerals like Talc and Serpentine Interfere with Nickel Flotation? How to Cope?
Talc and serpentine interfere significantly. Talc floats naturally, diluting concentrate. Serpentine forms slimes that coat valuable minerals and increase pulp viscosity. Mitigation involves using specific depressants (e.g., CMC, guar gum) and potentially circuit modifications like desliming.
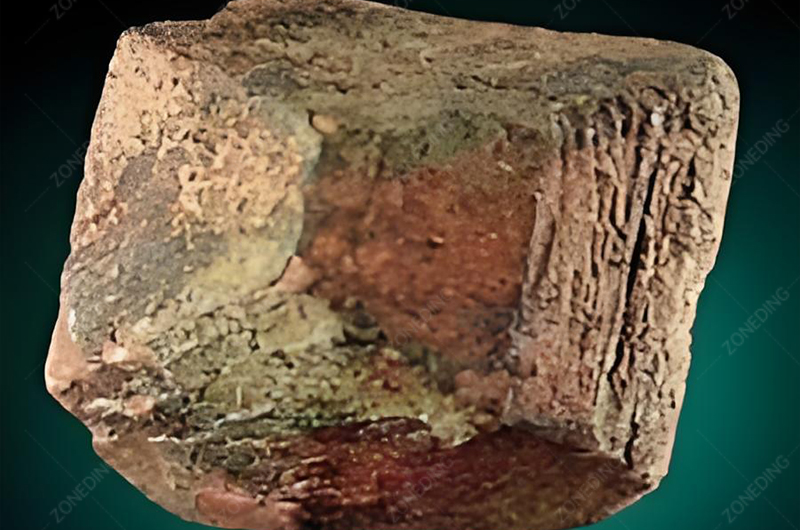

Dealing with Problematic Gangue
Certain silicate minerals commonly associated with nickel sulfide deposits can disrupt flotation performance.
- Talc:
- Problem: Talc has naturally hydrophobic surfaces, meaning it tends to float easily even without collectors. This leads to significant dilution of the nickel concentrate grade.
- Mitigation: Use specific depressant reagents that adsorb onto talc surfaces, making them hydrophilic. Common talc depressants include polysaccharides like Carboxymethyl Cellulose (CMC), guar gum, or dextrin. Precise dosage control is needed.
- Serpentine:
- Problem: Serpentine minerals tend to form very fine, fibrous particles (slimes) during grinding. These slimes can:
- Coat the surfaces of valuable nickel sulfide particles, preventing collector adsorption and hindering flotation.
- Increase the viscosity of the ore pulp, impairing bubble-particle collision and froth mobility.
- Consume reagents non-selectively.
- Mitigation:
- Depressants: Similar depressants used for talc (CMC, guar) can sometimes help mitigate serpentine effects.
- Desliming: Removing the ultra-fine slime fraction before flotation using techniques like hydrocycloning (Hydrocyclone) can be effective but may also lead to loss of fine nickel values if not carefully controlled.
- Circuit Design: Adjusting flotation cell hydrodynamics and froth handling systems to manage higher viscosity pulps.
- Problem: Serpentine minerals tend to form very fine, fibrous particles (slimes) during grinding. These slimes can:
Controlling problematic gangue like talc and serpentine often requires adding specific reagents and may necessitate adjustments to the standard flotation circuit design. Identifying their presence through mineralogy early on is crucial for planning effective mitigation strategies.
For Laterite Nickel Ore: Why Are Traditional Methods (like Flotation) Often Ineffective?
Flotation fails for laterites because the nickel is not present as distinct sulfide minerals. Instead, it’s chemically locked within the crystal structure of oxide or silicate minerals (like goethite, serpentine). Standard flotation chemistry doesn’t work on these mineral types.
Why Flotation Hits a Wall
The fundamental difference in how nickel occurs makes flotation unsuitable for laterites.
- No Sulfide Target: Flotation, as typically applied to nickel, relies on collectors that chemically bond to the surface of sulfide minerals like pentlandite. Laterite ores lack these sulfide minerals.
- Nickel’s Hiding Place: In laterites, nickel atoms substitute for iron or magnesium atoms within the atomic structure of the host minerals (iron oxides in limonite, magnesium silicates in saprolite). There is no discrete nickel mineral surface for standard collectors to attach to.
- Lack of Physical Contrast: Furthermore, the physical properties (density, magnetism) of the nickel-bearing laterite minerals are very similar to the bulk of the associated gangue material. This makes physical separation methods like gravity separation (Shaking Table, Spiral Chute) or magnetic separation (Magnetic Separator) largely ineffective for concentrating the nickel.
- Need for Chemical Attack: To extract nickel from laterites, the chemical bonds holding it within the host mineral lattice must be broken. This requires aggressive chemical processes like high-temperature smelting (pyrometallurgy) or strong acid leaching (hydrometallurgy).
Therefore, attempting to apply traditional sulfide flotation techniques to laterite ores is fundamentally flawed due to the entirely different way nickel is hosted in the ore.
What Physical Pre-treatment/Upgrading Can Be Done on Laterite Nickel Ore? (Limitations of Washing, Screening, Gravity)
Simple physical pre-treatment like washing (Sand Washing Machine) and screening (Vibrating Screen) can be highly valuable for laterites. They can remove coarse barren rocks and sometimes separate finer, richer fractions, effectively upgrading the feed to metallurgical plants. Gravity/magnetic methods remain largely ineffective.
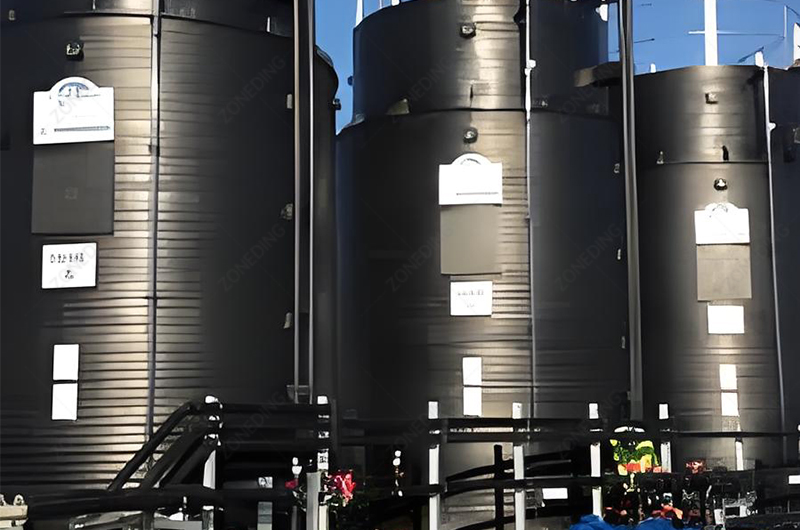
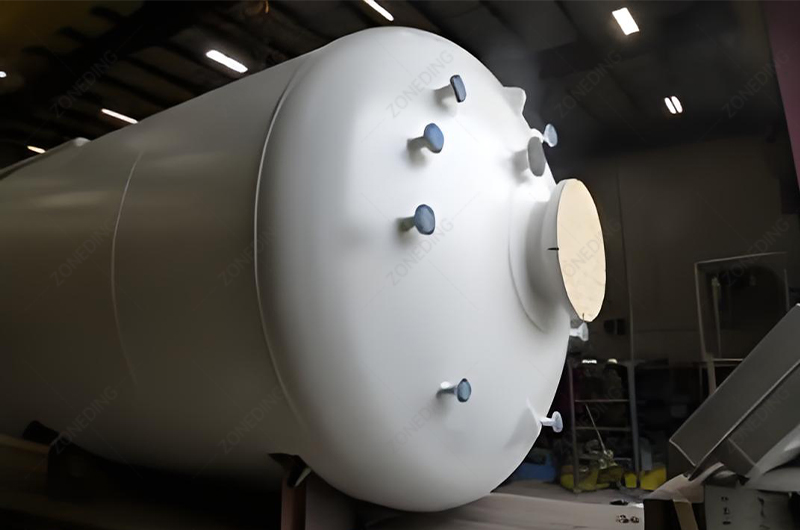
The Underestimated Value of Preparation
While high-ratio concentration isn’t feasible, preparing the laterite feed physically can significantly improve the economics of downstream chemical processing.
- Washing/Scrubbing: Laterite ores are often very clay-rich. Vigorous washing using equipment like rotary scrubbers or log washers breaks down clay lumps and removes sticky fines that can interfere with handling and downstream processes. ZONEDING offers relevant washing technology (Sand Washing Machine).
- Screening: This is often the most beneficial step.
- Removing Oversize Waste: Laterite deposits frequently contain large boulders or pebbles of barren bedrock or quartz. Screening (Vibrating Screen) these out before they enter the expensive leaching or smelting process significantly upgrades the feed’s nickel content on a tonnage basis. This reduces the volume of material needing chemical treatment, saving energy, reagents, and capital costs per unit of nickel.
- Size Fractionation: Sometimes, nickel distribution varies with particle size. For instance, the iron-rich limonite fraction (often targeted by HPAL) might be concentrated in finer sizes, while the magnesium-rich saprolite (often targeted by RKEF) might be coarser or more competent. Screening can potentially separate these fractions for optimized downstream processing or blending.
- Limited Gravity/Magnetic Use: As mentioned, the lack of significant density or magnetic contrast between the nickel-bearing minerals and gangue makes traditional gravity or magnetic separation largely ineffective for laterites.
Therefore, while not “concentration” in the sulfide sense, effective physical preparation – particularly screening – is a crucial and often highly economic first step in laterite nickel processing, simplifying downstream operations and reducing costs.
Laterite Nickel Processing: Why Does the Focus Usually Shift Directly to Hydro- or Pyro-metallurgy?
The focus shifts directly to hydrometallurgy or pyrometallurgy because nickel in laterites is chemically bound within host minerals. Only these chemical processes – leaching with acid (hydro) or smelting at high temperatures (pyro) – can break these bonds to extract the nickel.
Chemical Extraction is Key
Since physical methods can only prepare or modestly upgrade the ore, extracting the nickel requires breaking down the mineral structures chemically.
- Hydrometallurgy (Wet Processing): Involves dissolving the nickel using chemical solutions.
- High-Pressure Acid Leaching (HPAL): Uses sulfuric acid at high temperature (~250°C) and pressure (~40 bar) to dissolve nickel and cobalt, primarily from limonite ores. It’s complex and capital-intensive but can achieve high recoveries for suitable ores.
- Atmospheric Leaching (AL): Uses acid (usually sulfuric) at atmospheric pressure. Less aggressive, lower Ni recovery typically, potentially lower CAPEX, might be used for specific ore types or heap leaching scenarios.
- Pyrometallurgy (Smelting): Involves melting the ore at very high temperatures.
- Rotary Kiln-Electric Furnace (RKEF): The most common method for saprolite ores. Ore is dried and partially reduced in a kiln, then smelted in an electric furnace with a reductant (like coal) to produce ferronickel (an alloy of iron and nickel). Energy-intensive and sensitive to ore chemistry, especially SiO₂/MgO ratio.
- Other Smelting Routes: Such as smelting to produce nickel matte (a sulfide phase), might be used in specific integrated operations.
Because the nickel isn’t physically separable, these complex and energy/reagent-intensive chemical routes are the only viable options for extracting nickel from the bulk of therld’s laterite resources. The choice between hydro and pyro depends heavily on the ore’s specific chemistry (limonite vs. saprolite, impurity levels, MgO content) and project economics.
What Core Mining Machinery is Needed for Nickel Ore Processing/Pre-treatment?
Core machinery includes crushers (Jaw Crusher, Cone Crusher), grinding mills (Ball Mill, SAG), screens (Vibrating Screen), feeders (Vibrating Feeder), and conveyors. Laterite pre-treatment adds scrubbers/washers (Sand Washing Machine), while sulfide circuits require flotation cells (Flotation Machine) and conditioners (Mixer tanks).
Equipping the Nickel Plant
Regardless of the specific downstream process, the initial handling and preparation stages rely on robust mining machinery. ZONEDING provides many of these essentials.
Key Equipment for Nickel Ore Processing/Pre-treatment:
Process Stage | Key Equipment Types | ZONEDING Examples | Function |
---|---|---|---|
Comminution (Size Reduction) | Primary Crushers, Secondary/Tertiary Crushers, Grinding Mills (SAG, AG, Ball, Rod) | Jaw Crusher, Cone Crusher, Impact Crusher, Ball Mill, Rod Mill | Breaking ore for liberation (sulfide) or preparing feed size for leaching/smelting (laterite). |
Washing / Scrubbing (Laterite) | Rotary Scrubbers, Log Washers | Similar principles to Sand Washing Machine technology | Breaking down clays, removing slimes, preparing laterite for screening. |
Sizing & Classification | Vibrating Screens, Hydrocyclones, Spiral Classifiers | Vibrating Screen, Hydrocyclone, Spiral Classifier | Controlling particle size in grinding circuits (sulfide), removing oversize waste or classifying fractions (laterite). |
Flotation (Sulfide) | Flotation Cells (Mechanical, Column), Conditioning Tanks | Flotation Machine, Mixer tanks | Selectively recovering nickel sulfide minerals into a concentrate. Core of sulfide processing. |
Magnetic Separation (Sulfide) | Low & High Intensity Magnetic Separators | Magnetic Separator | Removing magnetic pyrrhotite to clean feed or concentrate. |
Material Handling | Feeders, Conveyors, Pumps | Vibrating Feeder, Belt Conveyors, Slurry Pumps | Transporting ore, slurry, and reagents throughout the plant. |
Dewatering | Thickeners, Filters | High Efficiency Concentrator, Filter Presses, Vacuum Filters | Removing water from final concentrate (sulfide) or tailings/residues (both types) before storage or transport. |
Reliability and efficiency are paramount for this core equipment, which often operates under demanding conditions. Choosing experienced suppliers like ZONEDING ensures access to machinery built for the rigors of nickel ore processing.
From Sulfide and Laterite Processing Perspectives, What Are the Main Environmental Challenges?
Sulfide processing faces major challenges with potential acid rock drainage (ARD) from sulfur-bearing waste/tailings and managing SO₂ emissions during smelting. Laterite processing deals with large land disturbance, managing vast tailings volumes (especially acidic HPAL residues), and high energy consumption, particularly for RKEF smelting.
Environmental Stewardship in Nickel Production
Both major nickel processing routes present distinct environmental challenges requiring proactive management.
- Sulfide Ore Processing:
- Acid Rock Drainage (ARD): Waste rock and tailings contain residual sulfide minerals (pyrite, pyrrhotite). When exposed to air and water, these oxidize to form sulfuric acid, which can leach heavy metals into surrounding water bodies. Prevention involves water management, potential use of covers or liners for waste storage, and water treatment.
- Smelter Emissions (SO₂): Smelting sulfide concentrates releases sulfur dioxide (SO₂), a major contributor to acid rain. Modern smelters require sophisticated gas capture and cleaning systems (e.g., producing sulfuric acid as a byproduct) to meet emission regulations.
- Reagent Handling: Safe storage, handling, and disposal/treatment of flotation reagents are necessary.
- Laterite Ore Processing:
- Land Disturbance: Laterite deposits are typically shallow and spread over large areas, requiring significant surface mining and land clearing. Progressive rehabilitation is essential.
- Tailings/Residue Management: Both HPAL and RKEF generate large volumes of waste material.
- HPAL Residues: Can be acidic and contain residual metals, requiring neutralization and secure, lined storage facilities to prevent seepage. Solid/liquid separation and water management are critical.
- RKEF Slag: Generally more inert but produced in large volumes, requiring stable long-term storage.
- Energy Consumption: Pyrometallurgical routes like RKEF are very energy-intensive, contributing significantly to the carbon footprint. HPAL also requires significant energy for heat and pressure.
- Water Management: Controlling runoff, erosion, and managing process water loops are important due to the scale of operations.
Responsible environmental management, including robust waste and water management strategies, emission controls, and land rehabilitation plans, is integral to the sustainability and social acceptance of any nickel project.
How to Assess the Technical and Economic Feasibility of Different Nickel Processing Options?
Feasibility assessment requires detailed metallurgical test work on representative ore samples, development of process flowsheets, estimation of capital (CAPEX) and operating (OPEX) costs, analysis of product markets, and comprehensive financial modeling (NPV, IRR) considering ore-specific characteristics.
Making the Right Investment Decision
A thorough feasibility study is essential before committing significant capital to a nickel project. Key components include:
- Ore Characterization: Detailed geological modeling, mineralogical analysis (identifying nickel minerals, gangue, impurities), and chemical assays. This determines if it’s sulfide or laterite, and its specific subtype (limonite/saprolite ratio, SiO₂/MgO ratio, contaminants).
- Metallurgical Test Work: Extensive laboratory and potentially pilot-scale testing to:
- Sulfide: Determine liberation size, flotation response, optimal reagent scheme, achievable recovery and concentrate grade, Cu/Ni separation efficiency, PGM recovery potential.
- Laterite: Determine amenability to leaching (acid consumption, kinetics, Ni/Co extraction) or smelting (energy requirements, slag behavior, Ni recovery), effectiveness of physical upgrading, Co recovery potential.
- Process Design & Engineering: Developing a detailed flowsheet, sizing major equipment, creating plant layout, and estimating infrastructure requirements.
- Capital Cost (CAPEX) Estimation: Estimating the cost of equipment, construction, engineering, infrastructure, and contingencies. HPAL plants typically have very high CAPEX.
- Operating Cost (OPEX) Estimation: Estimating ongoing costs for power, fuel, reagents (acid is a major cost for HPAL), labor, maintenance, water, and waste management. RKEF has high energy costs; HPAL has high acid and maintenance costs.
- Market Analysis & Revenue Projection: Determining the likely product (Ni concentrate, FeNi, MHP/MSP), expected prices, smelter terms or refining costs, penalties for impurities, and credits for byproducts (Co, Cu, PGMs).
- Environmental & Social Impact Assessment (ESIA): Assessing risks and mitigation costs.
- Financial Modeling: Integrating all costs and revenues to calculate Net Present Value (NPV), Internal Rate of Return (IRR), payback period, and performing sensitivity analyses on key variables (metal prices, costs, recovery).
A comprehensive feasibility study, grounded in solid test work and realistic cost/market assumptions, provides the basis for informed investment decisions in the complex nickel industry.
What Are ZONEDING MACHINE Advantages?
Critically, choose partners with proven, specific expertise in the correct processing route for your ore type – either sulfide flotation or laterite hydro/pyro-metallurgy. Assess their track record, understanding of specific challenges (e.g., Cu-Ni separation; HPAL materials; RKEF optimization), equipment robustness, and ability to support byproduct recovery.
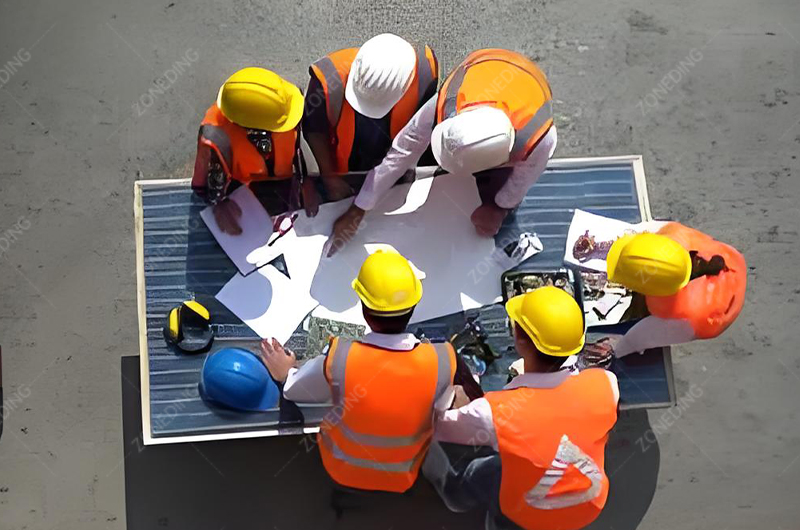
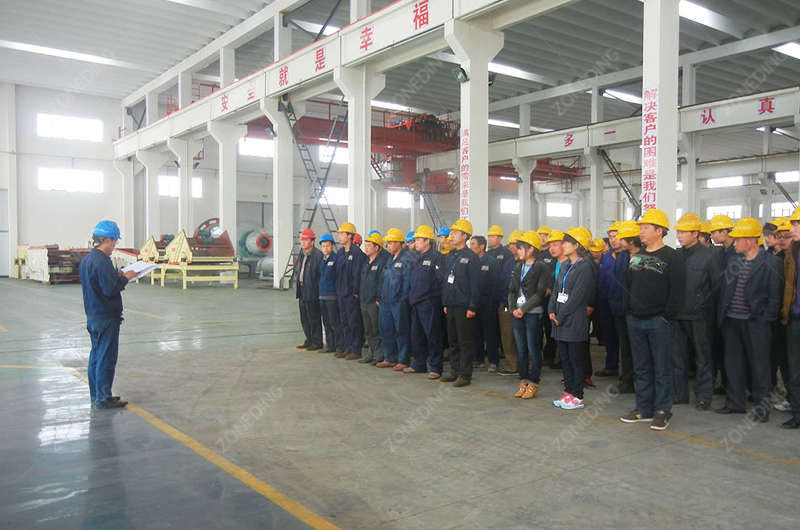
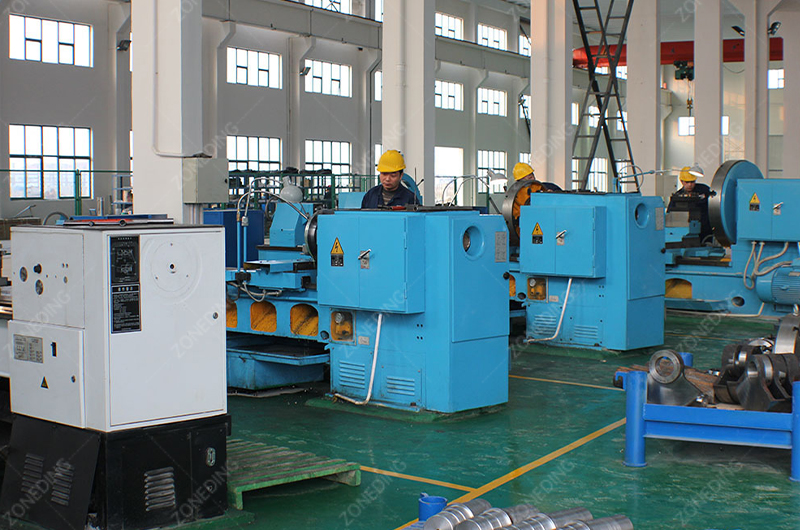
Advantages of ZONEDING MACHINE
The highly specialized nature of nickel processing demands experienced partners. Key criteria include:
- Route-Specific Expertise: This is paramount.ZONEDING has experience on sulfide flotation, HPAL or RKEF, and vice-versa. ZONEDING offers record with projects similar to yours (sulfide OR laterite).
- Deep Technical Understanding: ZONEDING understands the nuances:
- For Sulfides: Expertise in fine grinding, complex flotation chemistry (Cu-Ni separation, pyrrhotite/talc rejection), PGM behavior.
- For Laterites: Expertise in materials handling for sticky ores, washing/screening effectiveness, high-temperature materials (RKEF), corrosion-resistant materials (HPAL ), specific leaching/smelting chemistry (SiO₂/MgO impacts), solid-liquid separation challenges (HPAL).
- Proven Equipment Performance: Especially for the demanding conditions in laterite processing (abrasion, corrosion, high temperature), seek suppliers with robust, reliable equipment demonstrated in relevant applications. ZONEDING provides durable foundational equipment like crushers, mills, and screens suitable for the initial stages of either route.
- Testing & Pilot Plant Capabilities: ZONEDING has strong capabilities for comprehensive ore testing to tailor the solution.
- Byproduct Recovery Focus: ZONEDING has experience and approach to incorporating the recovery of valuable byproducts like Cobalt (from both ore types) and PGMs (from sulfides) into the flowsheet design.
- Lifecycle Support:ZONEDING has capacity for installation, commissioning, training, spare parts, and ongoing technical support.
Choosing partners based on demonstrated expertise directly relevant to your specific nickel ore type and chosen processing route significantly de-risks the project and enhances the likelihood of operational success. ZONEDING is your reliable partner.
Conclusion
Nickel processing is sharply divided: sulfide ores rely on flotation, while laterites demand hydro or pyrometallurgy. Understanding this fundamental difference is the first critical step. Success then depends on mastering the specific technical challenges of the chosen route and partnering with experienced technology and equipment providers.