Cobalt Ore Processing Plant Solutions
Cobalt ore is typically found in association with various minerals, such as copper-cobalt ore, nickel-cobalt ore, iron-bearing cobalt ore, and manganese-cobalt ore. These ores may contain impurities and harmful substances like sulfur and arsenic.
How is Cobalt Value Unlocked Through Processing from Ore to High-Purity Products?
Cobalt’s value is unlocked through a multi-stage process. This typically involves crushing and grinding the ore, concentrating the cobalt minerals (beneficiation), dissolving the cobalt (leaching), removing impurities (purification), and finally recovering the cobalt as a high-purity metal or chemical salt.
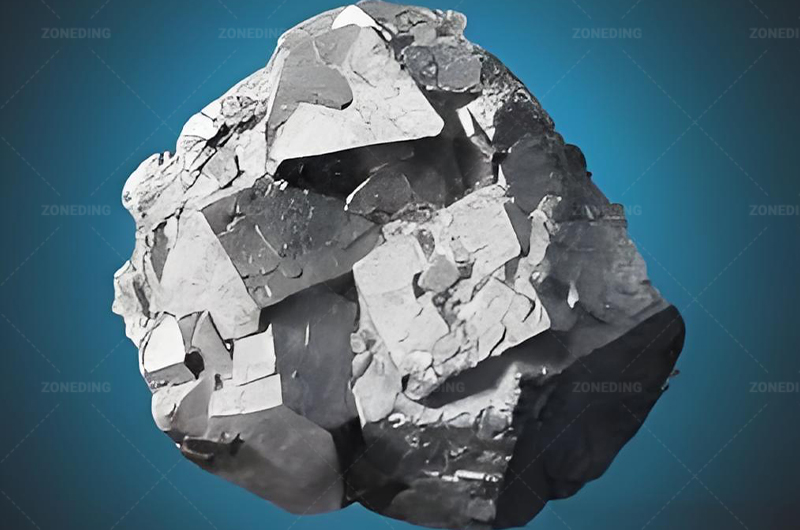
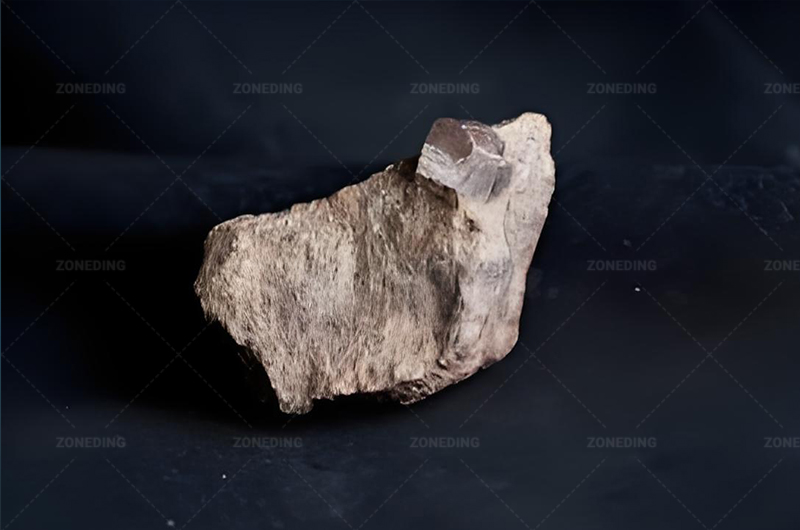
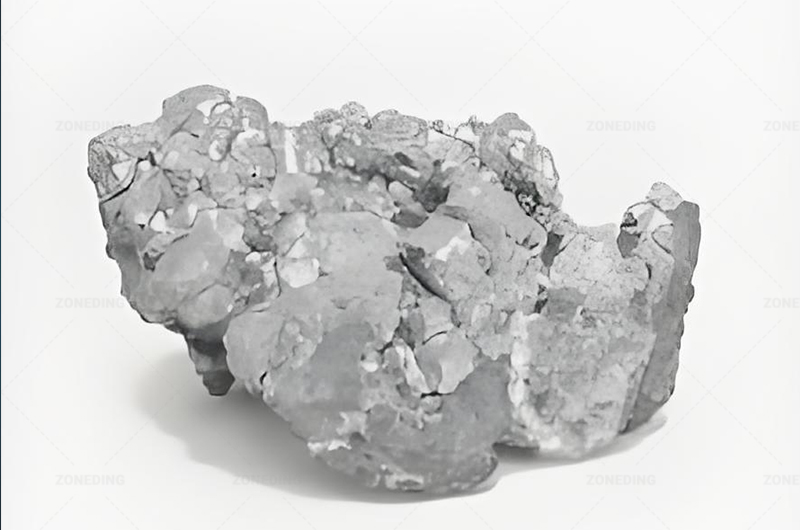
Extracting cobalt isn’t just about mining; the real challenge and value creation lie in the processing. It requires understanding your specific ore and applying the right technologies in the correct sequence.
Why is Cobalt Processing So Important Today? (Beyond Just Mining)
Processing is vital because raw cobalt ore has almost no direct use. It must be processed to concentrate the cobalt, remove harmful impurities, and convert it into the specific high-purity chemical forms required by industries like battery manufacturing.
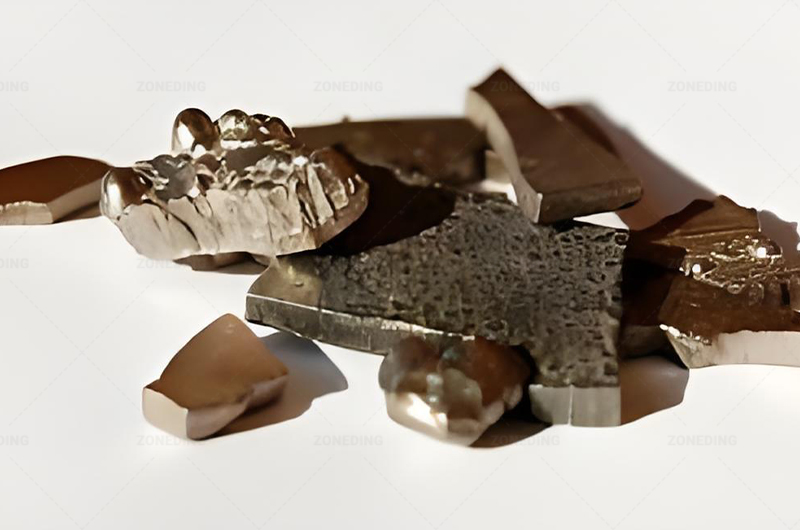
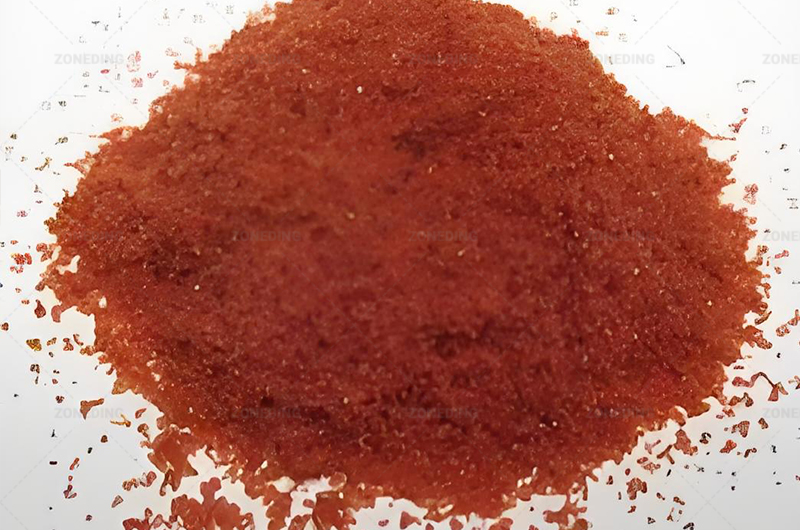
Transforming Rock into Technology Metals
Mining is just the first step. Processing is where the true value is unlocked and where the material becomes usable for modern applications.
- Meeting Market Demand: Industries, especially electric vehicle battery makers, need cobalt with extremely high purity (often >99.8% Co). Raw ores contain many other elements like copper, nickel, iron, manganese, and sometimes arsenic. Processing removes these contaminants.
- Increasing Concentration: Cobalt often occurs in low percentages within the ore. Processing significantly increases the cobalt concentration, making later chemical treatment steps more efficient and economically viable. Sending low-grade ore directly to chemical processing is usually too expensive.
- Creating Usable Forms: The market requires cobalt as specific products: pure metal sheets (cathodes), cobalt sulfate solutions, cobalt carbonate powders, etc. Processing converts the natural cobalt minerals into these standardized, sellable forms.
- Managing Associated Metals: Cobalt processing is rarely just about cobalt. The strategy heavily depends on how to efficiently separate and often recover valuable byproducts like copper and nickel, which frequently occur alongside cobalt. Handling these associated metals correctly is crucial for the project’s overall economics.
Therefore, processing is the essential bridge connecting a geological resource to its high-value, high-technology end uses.
What Type is My Cobalt Ore, and How Does it Impact Processing?
The ore type is critical. Oxide ores (like heterogenite) often need direct leaching with a reducing agent. Sulfide ores (like carrollite) usually require flotation first. Arsenide ores (like cobaltite) present major arsenic management challenges during processing.
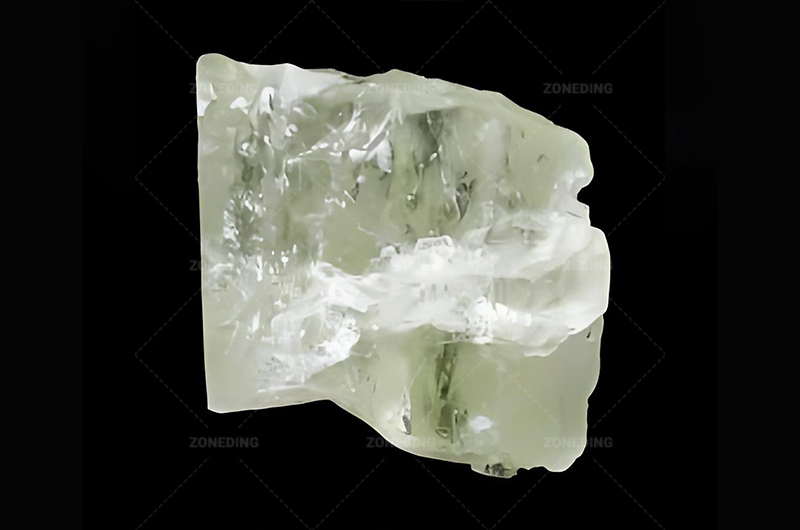

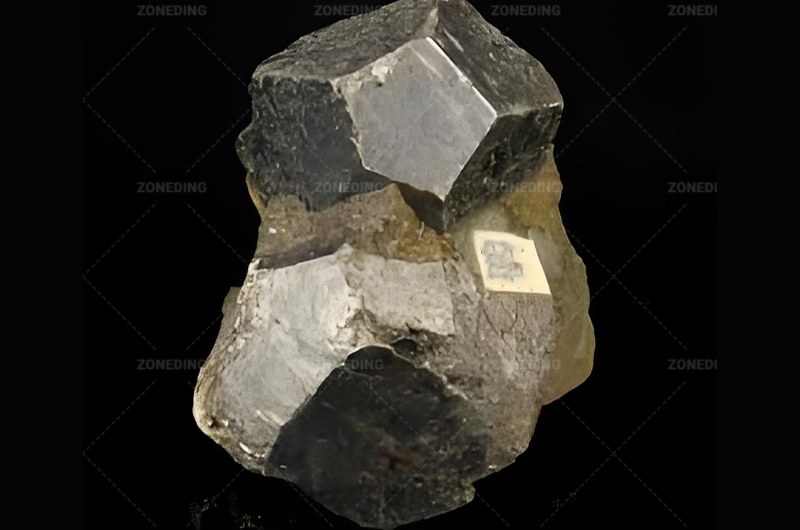
Ore Mineralogy Guides the Flowsheet
The specific mineral hosting the cobalt dictates the most suitable processing route. Knowing your ore type is fundamental.
Oxide Ore Challenges
Oxide minerals like Heterogenite (often containing Cobalt(III)) are common, particularly in the Copperbelt region. They are typically treated hydrometallurgically (leaching). A key challenge is that Cobalt(III) doesn’t dissolve easily in standard acid leaching. You often need to add a reducing agent (like sulfur dioxide or sodium metabisulfite) and carefully control the solution’s oxidation-reduction potential (ORP) to convert Co(III) to soluble Co(II) . Also, oxide ores can contain carbonate minerals, which consume large amounts of acid, significantly increasing operating costs.
Sulfide Ore Processing Focus
Sulfide minerals like Carrollite (Cu-Co-Ni sulfide) or Linnaeite (Co-Ni sulfide) are primary cobalt sources. These ores are almost always treated by froth flotation first. The goal is to physically separate the valuable sulfide minerals from the waste rock (gangue). A major challenge here is often the selective separation of copper sulfides from cobalt/nickel sulfides, as they have similar flotation properties. The resulting concentrate might then be leached (sometimes requiring aggressive conditions like pressure leaching) or smelted.
Arsenide Ore Management
Minerals like Cobaltite (CoAsS) or Skutterudite contain arsenic, a toxic element. Processing these ores requires extreme care. Often, roasting is employed early in the process to volatilize the arsenic, which must be captured safely. Leaching and waste disposal also require specialized procedures to prevent environmental contamination. Managing arsenic adds significant complexity and cost.
Furthermore, ore characteristics can change within the same deposit. Relying on a single initial analysis is risky. Continuous mineralogical monitoring linked to the mining plan acts like a “GPS” for the processing plant, allowing adjustments to grinding size, flotation reagents, or leaching conditions to maintain efficiency as the ore feed changes.
What Are the Core Steps in a Typical Cobalt Processing Flow? (Mine to Final Product)
A typical cobalt processing flowsheet includes: 1. Crushing & Grinding for size reduction, 2. Beneficiation to concentrate cobalt minerals, 3. Leaching to dissolve cobalt, 4. Purification to remove impurities, and 5. Recovery to get the final solid cobalt product.
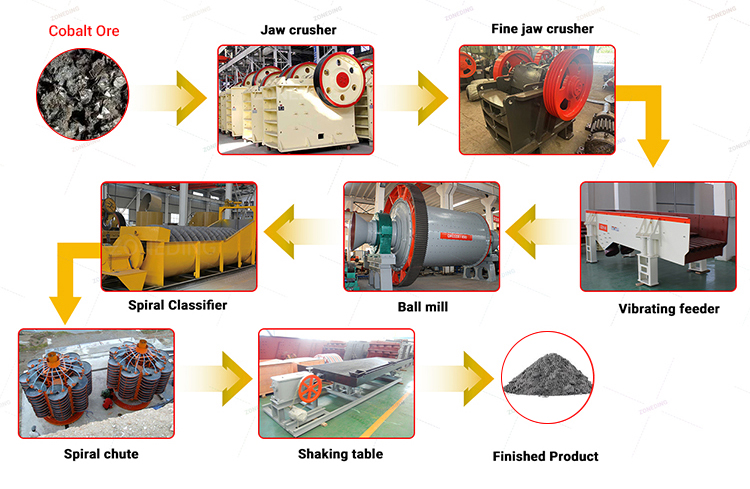
The Essential Sequence
While the specifics vary greatly based on the ore type and associated minerals, most cobalt operations follow these core stages:
- Size Reduction (Crushing and Grinding):
- Goal: Break down large run-of-mine ore and grind it fine enough to physically separate (liberate) the cobalt mineral particles from the surrounding waste rock particles.
- Equipment: Typically involves primary Jaw Crushers, followed by secondary/tertiary Cone Crushers or Impact Crushers, and finally grinding in Ball Mills or Rod Mills.
- Beneficiation (Concentration):
- Goal: Physically separate the liberated valuable cobalt minerals from the bulk of the waste rock (gangue). This increases the cobalt grade significantly before chemical processing.
- Methods: Froth Flotation Machine is dominant for sulfide ores. Gravity methods (Jigging Separator Machine, Shaking Table) or Magnetic Separators might be used for specific ore types or as pre-concentration steps.
- Leaching (Dissolution):
- Goal: Use chemical solutions (lixiviants) to dissolve the cobalt from the mineral concentrate (or sometimes directly from ore) into a liquid solution (pregnant leach solution or PLS).
- Methods: Sulfuric acid leaching is most common, often requiring heat, pressure, or chemical additives (reductants) for efficiency. Requires Mixer tanks for reaction.
- Purification (Impurity Removal):
- Goal: Selectively remove unwanted dissolved elements (like iron, manganese, copper, nickel, zinc) from the cobalt-rich leach solution to meet final product specifications, especially for battery grade.
- Methods: Often involves multiple steps like precipitation (adjusting pH to make impurities solid), solvent extraction (SX – using organic liquids to selectively grab metals), or ion exchange (IX – using resins).
- Recovery (Final Product Generation):
- Goal: Recover the purified cobalt from the solution as a solid, marketable product.
- Methods: Electrowinning (EW) produces pure cobalt metal plates. Chemical precipitation produces cobalt salts like carbonate or hydroxide. Crystallization can produce cobalt sulfate.
Each stage relies on the successful completion of the previous one. Understanding this flow is key to designing and operating a successful cobalt plant.
How to Effectively Crush and Grind Cobalt Ore for Optimal Liberation? (Choosing Crushers & Mills)
Effective size reduction involves staged crushing (e.g., Jaw Crusher then Cone Crusher) followed by controlled grinding (e.g., in Ball Mills or Rod Mills) to reach the “liberation size” – the point where most cobalt minerals are separate particles.
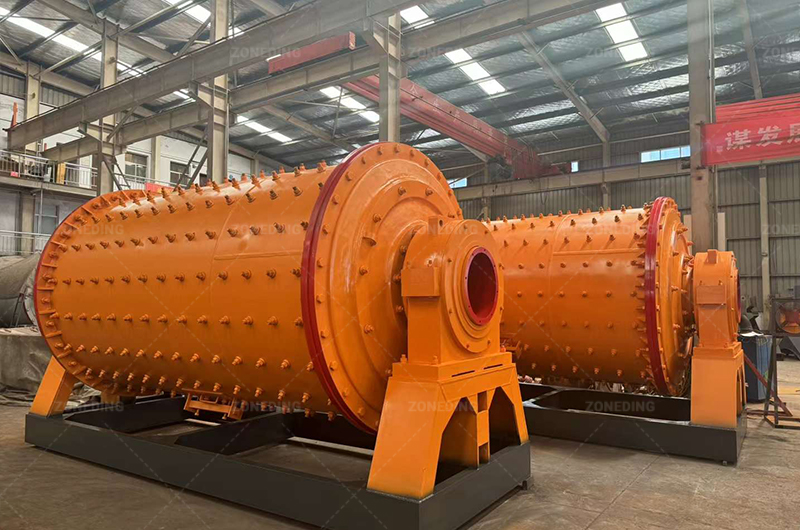
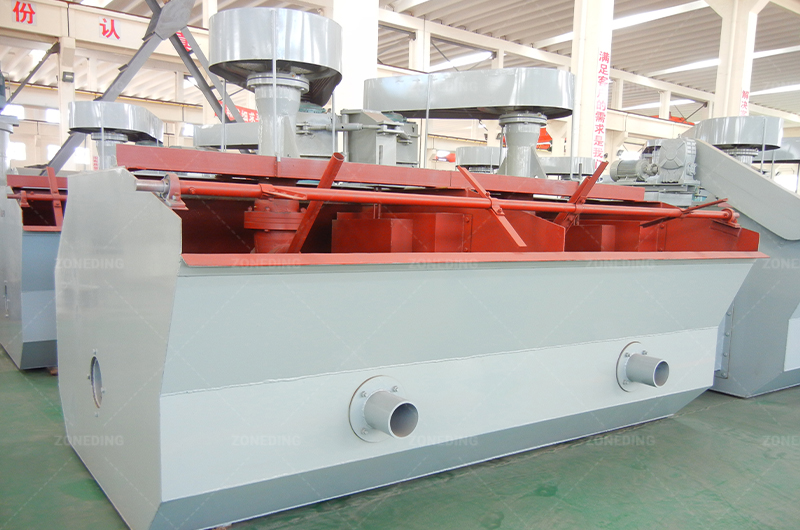
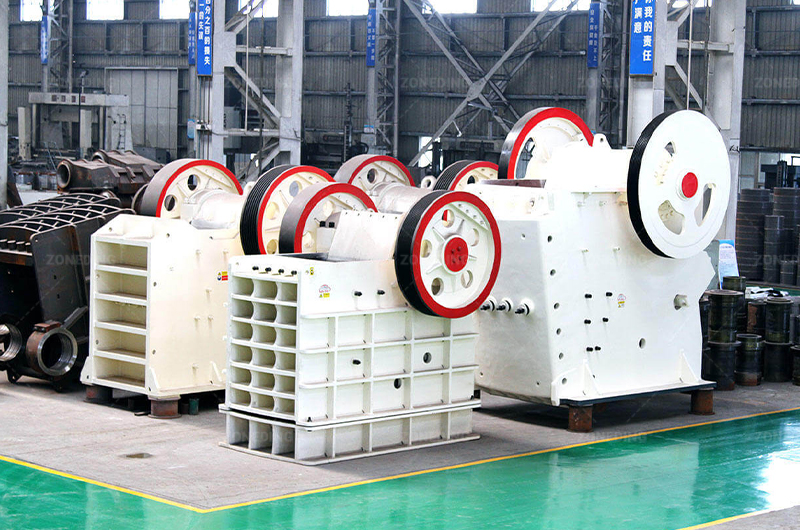
Balancing Liberation and Energy
The goal is optimal liberation without excessive energy consumption.
The Crushing Stages
Crushing typically happens in multiple stages using different types of Crushing Equipment:
- Primary Crushing: Uses robust machines like Jaw Crushers to handle large rocks directly from the mine (run-of-mine ore), reducing them to a size suitable for secondary crushing (e.g., <150mm).
- Secondary/Tertiary Crushing: Employs Cone Crushers (good for hard, abrasive ores) or sometimes Impact Crushers to further reduce the ore size (e.g., <20mm), preparing it for the grinding circuit. Sometimes a Mobile Stone Crusher offers flexibility.
The Grinding Stage
Grinding is usually done wet (mixed with water) in rotating mills to achieve the final target particle size needed for liberation.
- Mill Types: Ball Mills are very common for fine grinding. Rod Mills might be used for a coarser grind or specific particle shape needs. SAG (Semi-Autogenous Grinding) or AG (Autogenous Grinding) mills handle larger feed sizes but are typically used in very large operations.
- Liberation Size: This target size is determined through metallurgical testing (mineralogy ). Grinding finer than necessary wastes energy (a major cost) and can create ultra-fine particles (“slimes”) that hinder downstream processes like flotation or thickening (solid-liquid separation using equipment like a High Efficiency Concentrator). Grinding too coarse leaves cobalt locked in waste rock, reducing recovery.
- Closed Circuit: Grinding circuits often operate in “closed circuit” with classifiers like Hydrocyclones or Spiral Classifiers. These separate correctly sized particles from oversized ones, which are returned to the mill for further grinding, ensuring efficient size control.
Choosing the right combination of crushers and mills, like those provided by ZONEDING, tailored to your ore’s hardness, abrasiveness, and liberation characteristics, is crucial for efficient processing.
What Are the Main Methods to Concentrate Different Cobalt Ore Types? (Flotation, Gravity, Magnetic?)
Froth flotation is the most widely used method, especially for sulfide ores where cobalt is often associated with copper and nickel. Gravity and magnetic separation have niche applications for specific cobalt minerals or as pre-concentration steps.
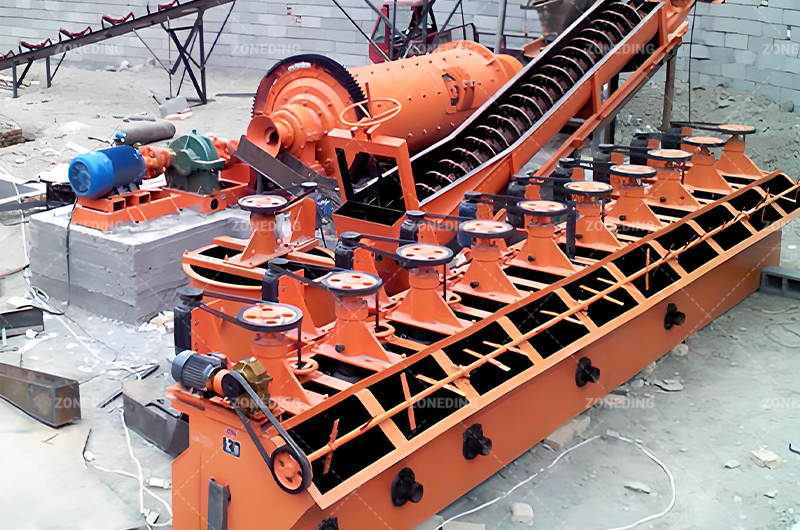
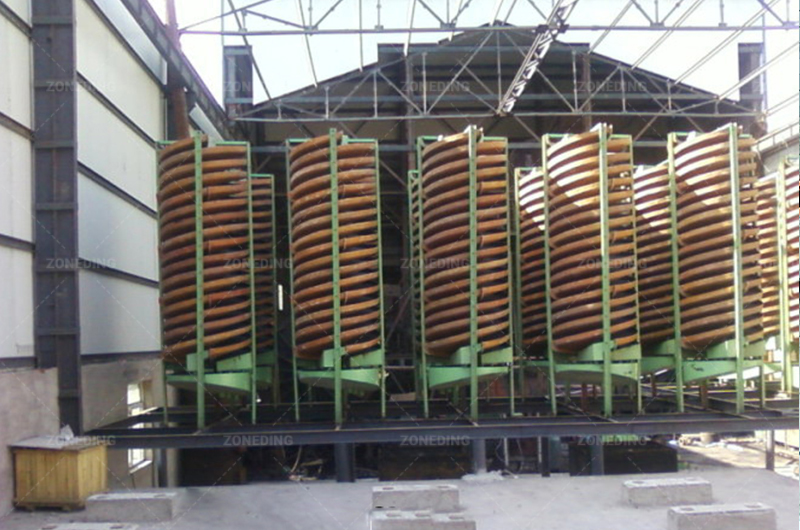
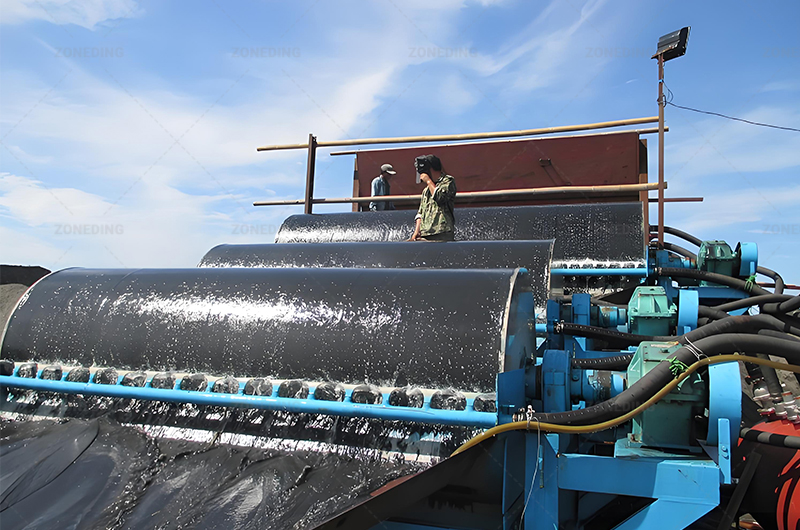
Upgrading the Ore Before Leaching
This physical separation stage, known as beneficiation or concentration, is a critical economic lever.
Froth Flotation
This is the workhorse for sulfide ores.
- How it Works: In a Flotation Machine, the ground ore slurry is mixed with specific chemical reagents. Collectors make the target mineral surfaces hydrophobic (water-repelling). Frothers create stable air bubbles. When air is introduced, the hydrophobic mineral particles attach to the bubbles and float to the surface, forming a froth that is collected as concentrate. Depressants are used to prevent unwanted minerals (like certain types of waste rock or sometimes even other sulfides) from floating.
- Cobalt Application: Essential for separating Co-bearing sulfides (like carrollite) from non-sulfide gangue. The major challenge is often achieving selectivity between different valuable sulfides, particularly separating copper minerals from cobalt/nickel minerals, which requires careful reagent selection and control.
Gravity Separation
This method uses differences in specific gravity (density) to separate minerals.
- Equipment: Includes Jigging Separator Machines, Spiral Chutes, and Shaking Tables.
- Cobalt Application: Less common for primary cobalt recovery but can sometimes be used if cobalt occurs as relatively dense, liberated minerals or to remove very dense gangue before flotation or leaching. It’s more effective on coarser particles than flotation.
Magnetic Separation
This technique separates minerals based on their magnetic properties.
- Equipment: Various types of Magnetic Separators (drum, belt, high-intensity).
- Cobalt Application: Direct magnetic separation of cobalt minerals is rare. It’s more often used to remove highly magnetic gangue minerals (like magnetite) before other processes, or potentially if cobalt is associated with magnetic minerals like pyrrhotite.
Effective beneficiation significantly reduces the mass going to the more expensive leaching and purification steps, saving on reagents, energy, and equipment size.
Leaching is Key: How to Efficiently Dissolve Cobalt from Concentrate? (Acid vs. Alkali vs. Bio?)
Sulfuric acid leaching is the dominant method globally for dissolving cobalt from various concentrates and ores. Success requires careful control of temperature, acidity (pH), and sometimes oxidation-reduction potential (ORP) using reductants.
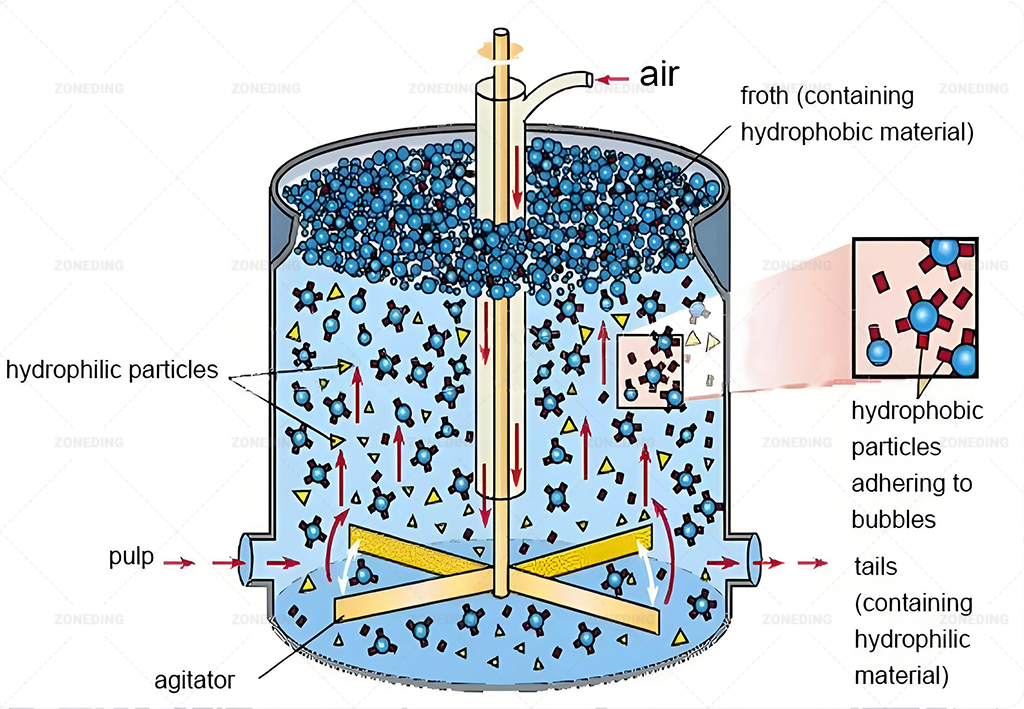
Chemical Extraction into Solution
Leaching uses a chemical solution (lixiviant) to selectively dissolve the target metal.
Acid Leaching (Sulfuric Acid)
This is the most common approach for both oxide and sulfide cobalt sources (sulfides often require pre-treatment like roasting or pressure oxidation, or direct aggressive leaching).
- Process: The concentrate is mixed with dilute sulfuric acid in agitated Mixer tanks, often at elevated temperatures (e.g., 60-80°C atmospheric leach, or much higher under pressure).
- Challenges:
- Acid Consumption: Gangue minerals, especially carbonates (like calcite or dolomite), can consume large amounts of expensive acid. Accurate mineralogy is needed to predict acid use.
- Reductant Need: For oxide ores containing Cobalt(III) (e.g., heterogenite), a reducing agent (like SO2 gas or sodium metabisulfite) must often be added to convert it to the soluble Cobalt(II) form.
- ORP Control: Maintaining the correct Oxidation-Reduction Potential (ORP) is crucial, especially when using reductants. Too high ORP means poor Co(III) leaching; too low ORP might dissolve excessive iron or manganese, complicating purification. Requires careful monitoring and reagent dosing.
- Impurity Dissolution: Acid dissolves not just cobalt but also copper, nickel, iron, manganese, zinc, magnesium etc., necessitating extensive downstream purification.
Alkaline Leaching (Ammonia)
Uses ammonia-based solutions, sometimes used for specific nickel-cobalt laterites or complex ores. It’s more selective against iron and manganese but generally has slower kinetics and involves handling ammonia.
Bioleaching
Uses microorganisms to break down sulfide minerals and release metals. It has lower reagent costs but is very slow (months) and sensitive to conditions, mainly used for low-grade sulfides.
For most commercial cobalt operations, optimizing the conditions of sulfuric acid leaching (temperature, acid concentration, ORP, residence time) based on the specific concentrate feed is key to efficient cobalt extraction.
Tough Cu/Co or Ni/Co Separation? How to Selectively Separate and Purify Cobalt from Complex Leach Solutions? (SX vs. Precipitation vs. IX?)
Solvent extraction (SX) is the core technology for the difficult separation of cobalt from nickel and copper. Precipitation removes bulk impurities like iron first, while ion exchange (IX) can provide final polishing for trace element removal.
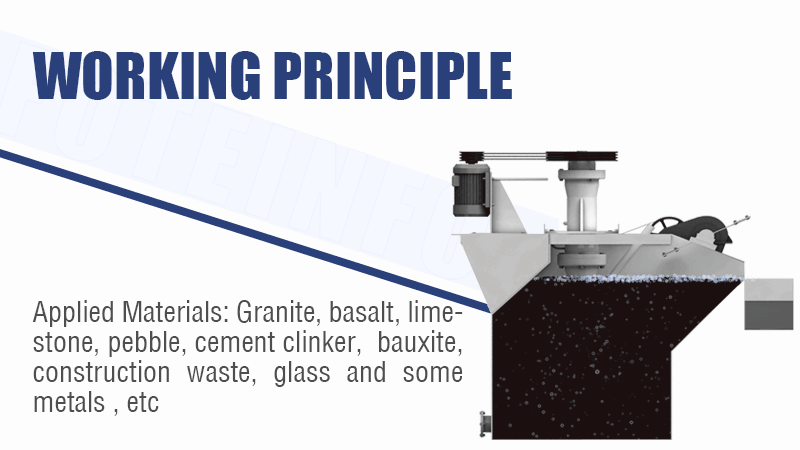
Refining the Cobalt Solution
Achieving parts-per-million purity levels requires a sophisticated multi-stage purification sequence.
Precipitation
This is often the first step to remove bulk impurities that interfere with later stages or consume expensive reagents.
- Iron/Aluminum Removal: By carefully raising the solution pH (e.g., adding limestone or lime), iron and aluminum precipitate as hydroxides and can be filtered off. Careful control is needed to avoid precipitating cobalt.
- Copper/Zinc Removal: Sometimes, copper and zinc can be selectively precipitated as sulfides by adding reagents like NaHS or H2S gas, or removed via other methods.
Solvent Extraction (SX)
This is the workhorse for separating chemically similar elements like cobalt, nickel, and copper.
- Process: The impure aqueous solution is mixed vigorously with a specific organic liquid containing an extractant chemical. The extractant selectively bonds with the target metal ion (e.g., copper first, then cobalt) and pulls it into the organic phase. The phases are allowed to separate (settle), and the metal-loaded organic phase moves on. Later, the metal is stripped back into a clean aqueous solution using a different chemical environment (e.g., stronger acid).
- Co/Ni Separation: This is often the most challenging SX step due to the similar chemistry of Co and Ni. It requires specific extractants (like Cyanex 272 or similar phosphinic acids) and precise control of pH and other conditions. Multiple stages are usually needed.
Ion Exchange (IX)
This uses solid resin beads with active chemical groups that selectively bind specific ions from the solution.
- Application: Often used as a final polishing step to remove trace impurities (like residual zinc, manganese, or critical elements like magnesium and calcium for battery grade) that SX might not remove effectively. It can also be used for primary separation in certain situations.
The exact combination and sequence of precipitation, SX, and IX stages depend heavily on the initial leach solution composition and the final desired product purity. Achieving battery grade requires meticulous removal of not just major metals but also specific trace elements.
How to Finally Obtain Battery-Grade or Other High-Purity Cobalt Metal or Salt Products? (EW vs. Precipitation?)
Electrowinning (EW) is used to produce high-purity cobalt metal cathodes directly from the purified solution. Chemical precipitation is used to produce cobalt salts like carbonate or hydroxide, often as intermediates or final products.
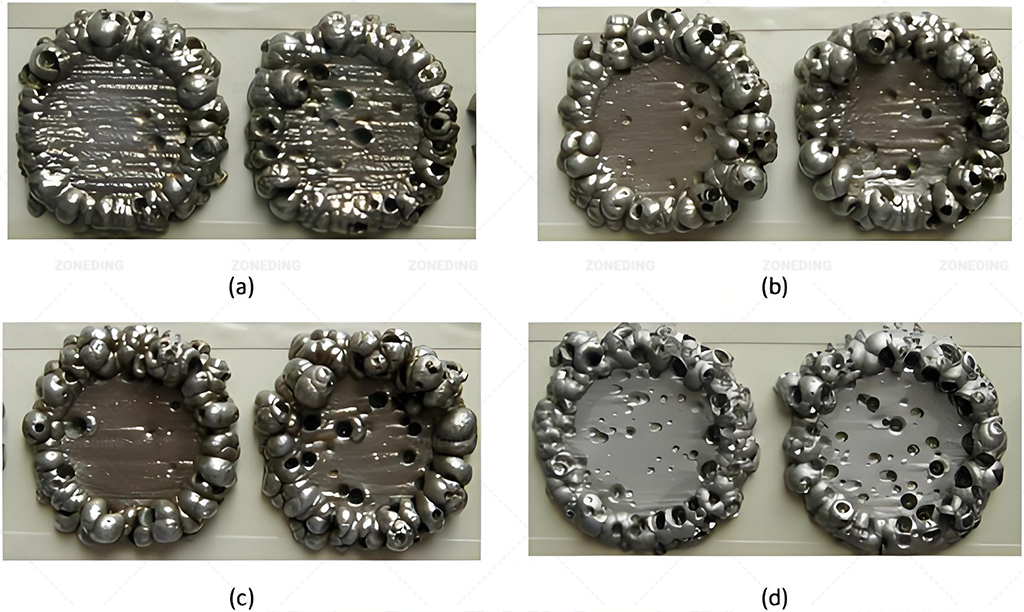
Recovering the Final Product
The final recovery method depends on the target market and product specifications.
Electrowinning (EW)
- Process: A direct electric current is passed through the highly purified cobalt sulfate solution in electrochemical cells. Pure cobalt metal (>99.8% or higher) deposits onto cathode blanks (often stainless steel), while water is oxidized at the anode.
- Product: High-purity cobalt metal cathodes.
- Considerations: Requires extremely pure electrolyte feed – impurities can ruin the deposit quality or lower current efficiency. It is energy-intensive. This is the standard method for producing cobalt metal.
Chemical Precipitation
- Process: A chemical reagent is added to the purified cobalt solution to cause the cobalt to precipitate out as a solid compound. Common reagents include sodium carbonate (soda ash) to produce cobalt carbonate (CoCO3), or sodium hydroxide (caustic soda) or magnesium oxide (MgO) to produce cobalt hydroxide (Co(OH)2).
- Products: Cobalt Carbonate or Cobalt Hydroxide powders/slurries.
- Considerations: Relatively simpler than EW. The purity of the precipitated salt directly depends on the purity of the feed solution. These precipitates are often sold as intermediates or can be re-dissolved and crystallized to produce high-purity cobalt sulfate (CoSO4·7H2O), another key battery material.
Crystallization
- Process: Specifically for producing cobalt sulfate, highly purified cobalt sulfate solution is evaporated under controlled conditions to form crystals (e.g., CoSO4·7H2O).
- Product: High-purity Cobalt Sulfate crystals.
The choice between EW and precipitation depends on market demand, downstream integration (e.g., direct use in battery precursor manufacturing), and the specific purity requirements, particularly the very low levels of certain impurities demanded for battery applications.
What Specific Environmental, Cost, and Technical Hurdles Need Special Attention When Processing Cobalt Ore?
Maximize prKey challenges include managing hazardous elements like arsenic, controlling high reagent (acid, reductants) and energy costs, achieving extreme purity while separating similar metals, managing water use and wastewater treatment, and handling variable ore feed.
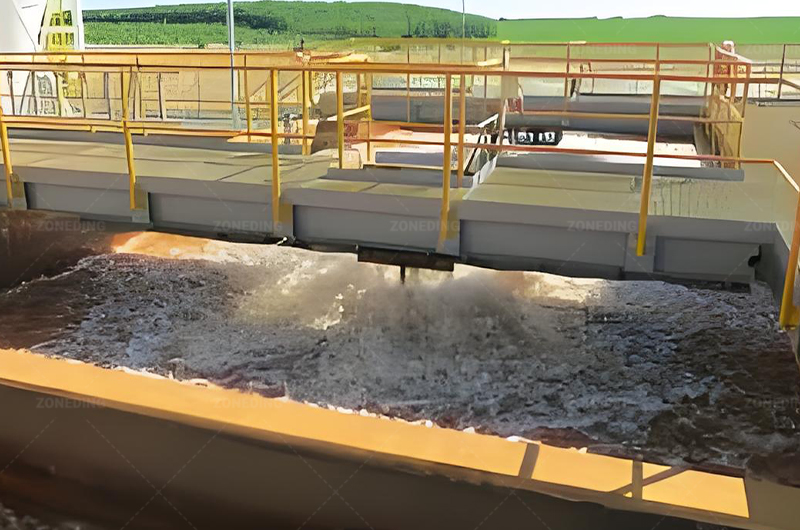
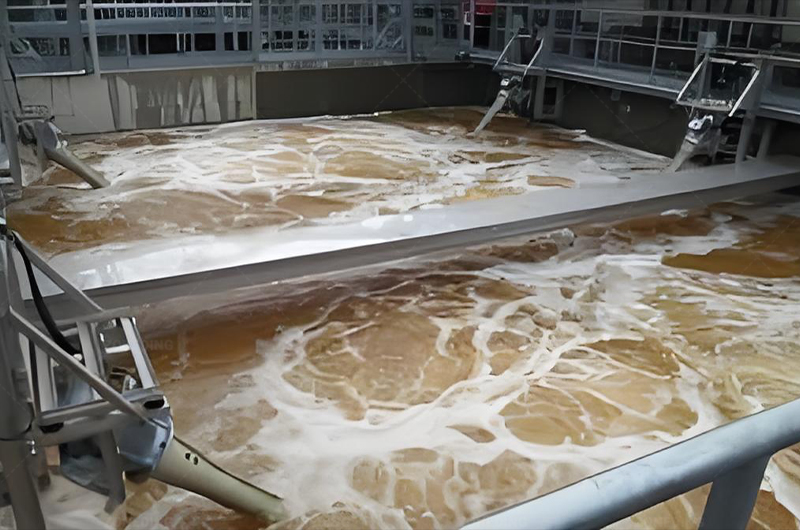
Major Roadblocks and Considerations
Processing cobalt successfully means navigating significant hurdles:
- Environmental and Safety
- Arsenic Management: If present in the ore, arsenic requires specialized handling, roasting fume capture, secure disposal of arsenic-bearing residues, and strict worker safety protocols.
- Tailings & Waste Rock: Large volumes of waste require stable, environmentally sound storage facilities to prevent acid rock drainage and metal leaching.
- Wastewater Treatment: Wet processing generates effluents containing residual metals, sulfates, chlorides, and reagents. Treatment to meet discharge standards can be complex and costly, often requiring multiple steps like neutralization, precipitation, and clarification. Water scarcity also drives the need for efficient water recycling, which can lead to impurity buildup if not managed carefully.
- Cost Control
- Reagent Consumption: Sulfuric acid, reductants (if needed), flotation chemicals, SX reagents, and neutralizing agents represent major operating costs. Optimizing their use is critical. Pre-concentration helps reduce downstream consumption.
- Energy Usage: Grinding, leaching (heating, agitation), ventilation, and especially electrowinning are energy-intensive processes. Energy efficiency is a key design and operational goal.
- Capital Costs: Building a complex hydrometallurgical plant with multiple purification stages requires significant upfront investment.
- Technical Complexity
- Feed Variability: Changes in ore mineralogy, grade, or impurity levels can wreak havoc on plant performance. Continuous monitoring and potentially dedicated pre-treatment for inconsistent feed like artisanal ore are crucial.
- Difficult Separations: Separating cobalt cleanly from chemically similar metals like nickel requires sophisticated process control and potentially complex SX circuits. Achieving ultra-low levels of specific trace impurities for battery grade adds another layer of difficulty.
- Process Control: Maintaining tight control over parameters like pH, ORP, temperature, and flow rates throughout the plant is essential for efficiency and purity. This requires skilled operators and robust instrumentation.
Addressing these challenges requires careful planning, robust engineering, experienced personnel, and a strong commitment to environmental responsibility from the outset.
When Choosing a Suitable Cobalt Processing Equipment Supplier-What Are Advantages of ZONEDINGMACHINE?
Prioritize suppliers with demonstrated expertise in cobalt or similar complex hydrometallurgical applications. Evaluate their customization capabilities, equipment durability for harsh conditions, process support, local service presence, and reliable after-sales support (spares, technical assistance).
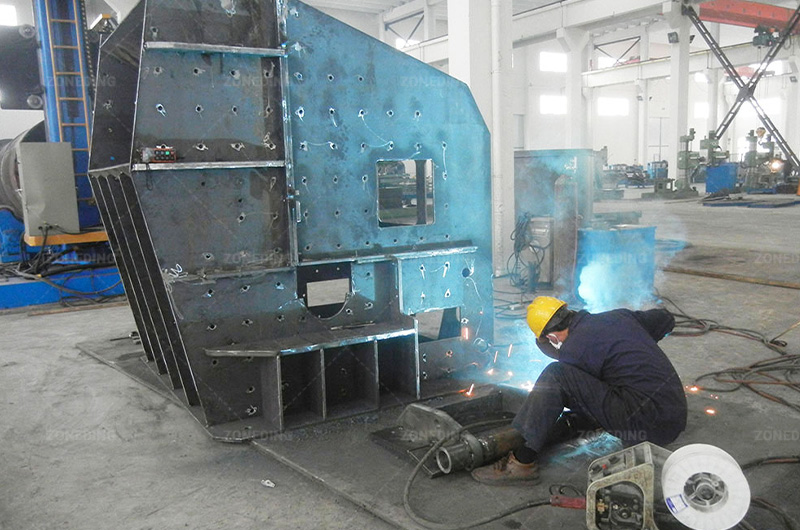
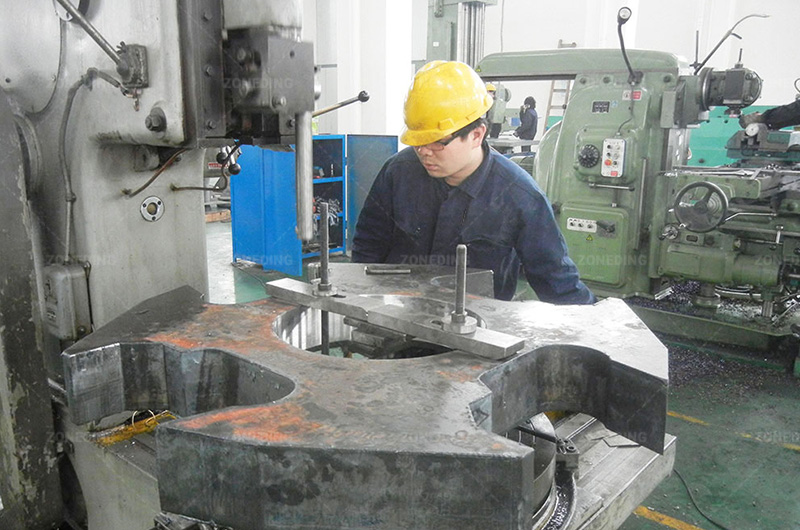
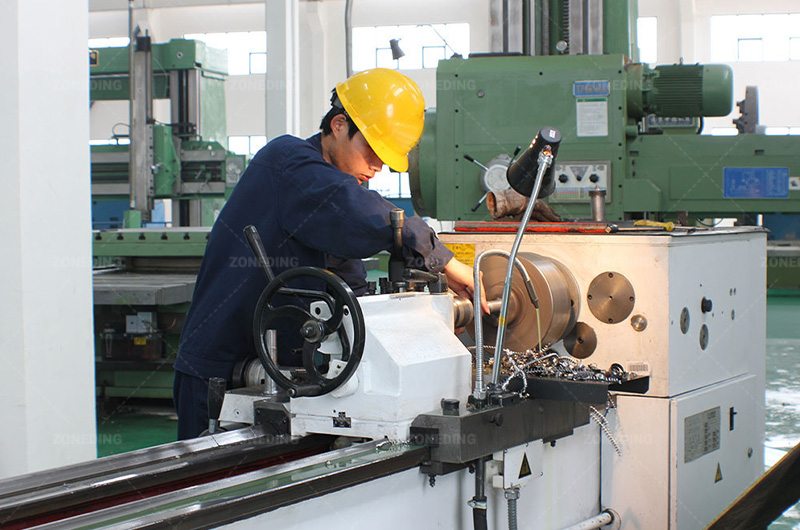
Selecting Your Equipment Partner
Choosing an equipment supplier is a long-term decision. Consider these factors:
- Relevant Experience: ZONEDINGMACHINE, with proven installations in cobalt processing and similar complex base metal circuits (e.g., Cu-Co, Ni-Co), can offers references and case studies relevant to your ore type and planned flowsheet.
- Customization and Engineering: Cobalt processes often require tailored solutions. ZONEDINGMACHINE, as a direct supplier, can modify equipment designs (e.g., materials of construction for corrosive leach solutions, specific Flotation Machine configurations for selective separation, robust Jaw Crushers for hard ore).
- Equipment Robustness: The processing environment can be highly corrosive (acidic) and abrasive. ZONEDINGMACHINE can ensure equipment like Ball Mills, pumps, Mixer tanks, and even Vibrating Screens uses appropriate materials (special alloys, rubber lining) for long service life.
- Process Integration: ZONEDINGMACHINE supplier can understand how their equipment fits within the entire flowsheet. ZONEDING can also supply integrated solutions, from Crushing Equipment to grinding and beneficiation circuits.
- After-Sales Service & Spares: This is critical, especially for remote operations. ZONEDINGMACHINE can provide timely technical support, troubleshooting assistance, and readily available spare parts for wear items.
- Installation & Commissioning Support: Proper installation and commissioning are vital for performance.ZONEDING MACHINE offers experienced technicians for supervision or turnkey installation.
- Total Cost of Ownership: Evaluate beyond the initial price. Consider energy efficiency, expected maintenance costs, spare parts pricing, and the overall durability and expected lifespan of the equipment. As a source supplier, ZONEDINGMACHINE gives the best price for machine.
Partnering with an experienced and reputable supplier like ZONEDING, who understands the intricacies of mineral processing and offers robust, customized equipment backed by reliable support, is essential for the long-term success of your cobalt operation.
Conclusion
Unlocking cobalt’s value requires navigating a complex processing path from ore to pure product. Success hinges on understanding your specific ore, selecting appropriate technologies, and partnering with experienced equipment suppliers.
Related notes
What is a Ball Mill Used For?
How to choose magnesium ore ball mill? The role and advantages of magnesium ore ball mill
Iron Fine Powder Ball Mill Application Scope
Phosphate ball mill working principle, structure, phosphate ball mill steel ball loading capacity
Should I use a ball mill or a rod mill to grind limestone?
Lithium pyroxene ball mill features, lithium ore ball mill price
loading…
已经是到最后一篇内容了!
Related Products
Ball Mill
Our ball mill are available in different styles and many models in each style to adapt to various grinding requirements.
Rod Mill
Rod MillRod Mill For SaleWorking Principle of Rod MillProduct Features of Rod MillRod Mill shipmentParameters of Rod MillRod millService Supportof Rod MillFAQRelated ProductsOur Rod Mill are available in different styles and numerous model sizes …
Ceramic Ball Mill
Ceramic Ball MillCeramic ball mill For SaleAdvantages of Ceramic ball millFunctional Advantages of Ceramic ball millApplication Scenarios of Ceramic ball millCeramic ball mill shipmentCeramic ball mill customer work siteParameters of Ceramic ball…
Flotation Machine
Flotation MachineFlotation Machine For SaleAdvantages of Flotation MachineFlotation Machine: Suitable Ore TypesStructure of flotation machinePrinciple of Flotation MachineFlotation ProcessParameters of Flotation Machineflotation machineAssembly s…
Spiral Classifier
Spiral classifiers can grade different particles in ore slurry during the metal beneficiation process as well as deslime and dehydrate in the washing operation.
Mixer
Introduction of MixerThe Application and Function of Agitating TankThe Working Principle of Agitating TankAgitating Tank ManufacturerGeneral SpecificationMixerFAQRelated Products Mixer Mixing barrel is mainly used in all kinds of metal mining in…
Wet Drum Magnetic Separator
Wet Drum Magnetic SeparatorWhat is wet drum magnetic separatorFeatures of Wet Drum Magnetic Separator:Structure of Wet Drum Magnetic SeparatorPrinciple of Wet Drum Magnetic SeparatorCustomer Case of Wet Drum Magnetic SeparatorSpecification of Wet…
Shaking Table
Shaking Table For SaleAdvantages of Shaking TableApplication of Shaking TablePrinciple and structure of shaking tableI. Working PrincipleII. Structural compositionParameters of shaking tableShaking Tableshaking table customer work siteFAQRelated P…
Gold Mine Wet Pan Mill
Wet Pan Mill for saleApplicationsWet Pan Mill AdvantagesProduct StructureWet Pan Mill Working PrincipleParameters of Wet Pan MillRelated Products Gold Mine Wet Pan Mill is a highly efficient, energy-saving and easy-to-ope…
Jigging Separator Machine
Jigging Machine for saleApplicationsProduct StructureWorking PrincipleParameters of Jigging MachineJigging Machine customer work siteRelated Products Jigging Machine(jig concentrator, jig machine, mineral jig, Jiggin…
loading…
已经是到最后一篇内容了!
We use cookies to ensure that we give you the best experience on our website. If you continue to use this site we will assume that you are happy with it.
OK
Privacy Policy