Antimony Ore Processing Plant Solutions
Antimony ore can be classified into antimony oxide and antimony sulfide. The main methods for its beneficiation are hand selection, gravity separation, and flotation.
Antimony ore beneficiation can be achieved through a combination of hand separation, gravity separation, and flotation techniques. Our antimony ore processing plants and equipment are designed to have strong adaptability and high recovery rates.
How Do We Unlock Antimony’s Value: From Ore to Metal, Facing Technical Hurdles and Finding Solutions?
Unlock antimony’s value needs through careful, specialized steps. The usual process involves crushing and grinding the ore. Then concentrate the antimony minerals, often using flotation or gravity methods. Next, extract the metal, typically by smelting. Finally, refine the antimony to meet market needs.
Antimony pictures
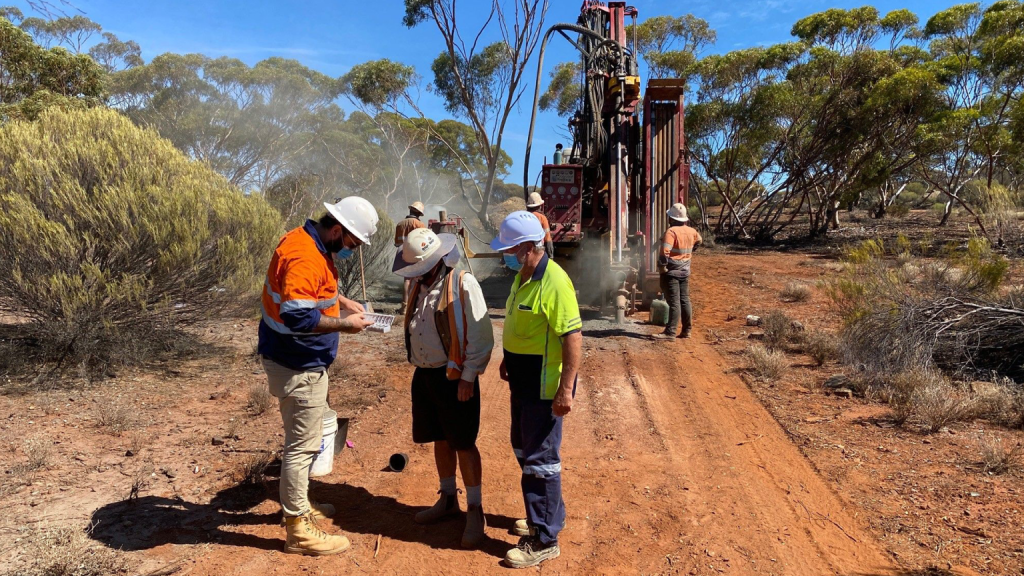
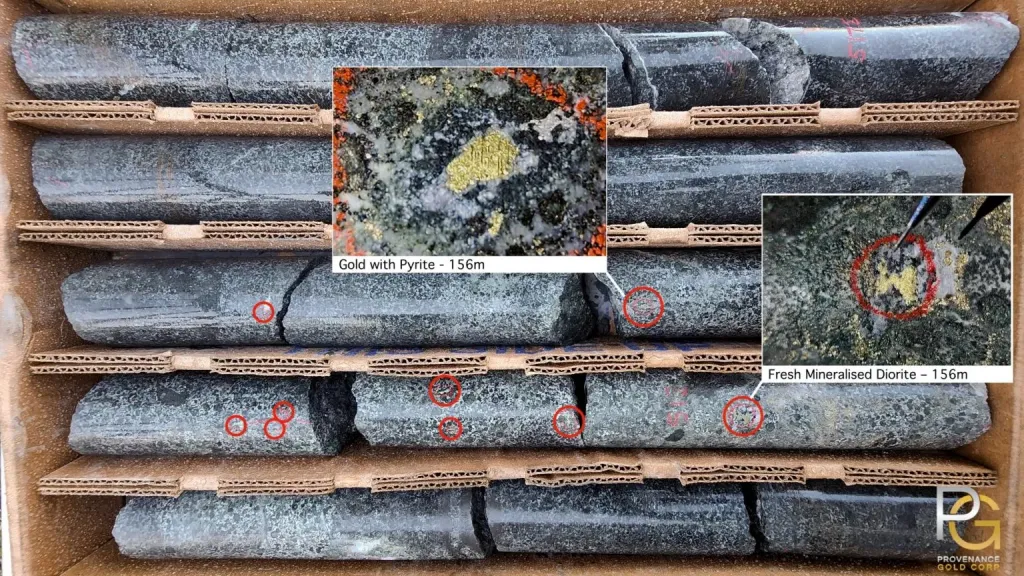
This journey needs good planning. It needs precise work. And it needs the right technology. Antimony ores have unique challenges.
Why is Specialized Antimony Ore Processing Crucial? (Driven by Antimony’s Application Value)
You know antimony is used in things like flame retardants and batteries. But why the need for specialized processing? Can’t standard methods work?
Specialized processing is crucial because antimony’s end uses demand specific chemical forms (metal grades, high-purity trioxide) and low levels of impurities. Processing concentrates the metal and removes harmful elements like arsenic, unlocking its value for these critical applications.
application
Meeting Tough Market Demands
Raw antimony ore, straight from the mine, cannot be used directly by industry. Specialized processing is vital for these reasons:
- Making it Concentrated: Antimony is often found in low amounts in the ore. Processing greatly increases the antimony percentage. This makes the later chemical steps possible and affordable.
- Removing Harmful Impurities: Many applications need very pure antimony. Flame retardants, for example, need high-purity Antimony Trioxide (Sb2O3). Alloys need specific metal grades. Impurities like arsenic and lead are very problematic. Processing gets rid of these unwanted elements.
- Creating the Right Form: Industries need antimony as metal blocks (ingots) of certain purity. Or they need it as specific chemical compounds like Sb2O3. Processing changes the natural minerals into these usable, sellable forms.
- Capturing the Gold: This is a very important point. Many antimony ores also contain gold. Often, this gold is present as tiny, hidden particles. In lots of these deposits, the gold is worth much more than the antimony itself. So, the processing plan must aim to recover as much gold as possible. Sometimes, you might even accept lower antimony recovery to get more gold. Focusing only on antimony and ignoring the gold is a big mistake that makes many projects fail economically. The whole plan, from grinding to extraction, must think about the total value of antimony and gold.
Specialized processing makes antimony useful for its unique applications. It also often needs to recover valuable partners like gold at the same time.
What Type is My Antimony Ore? (Stibnite vs. Oxide vs. Complex Ores & Impact on Processing?)
The ore type is extremely important. Stibnite, a sulfide mineral, is usually concentrated using froth flotation. Oxide ores need different methods, like smelting or leaching. Complex ores, especially those with arsenic (Insight #3) or gold (Insight #1), need specially designed processes.
types
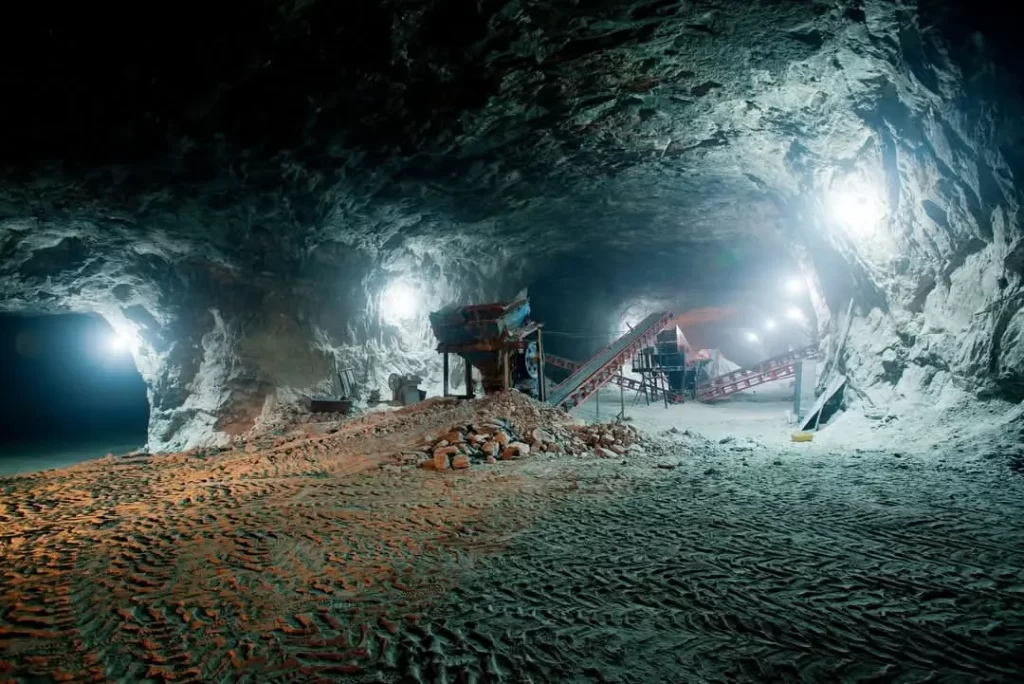
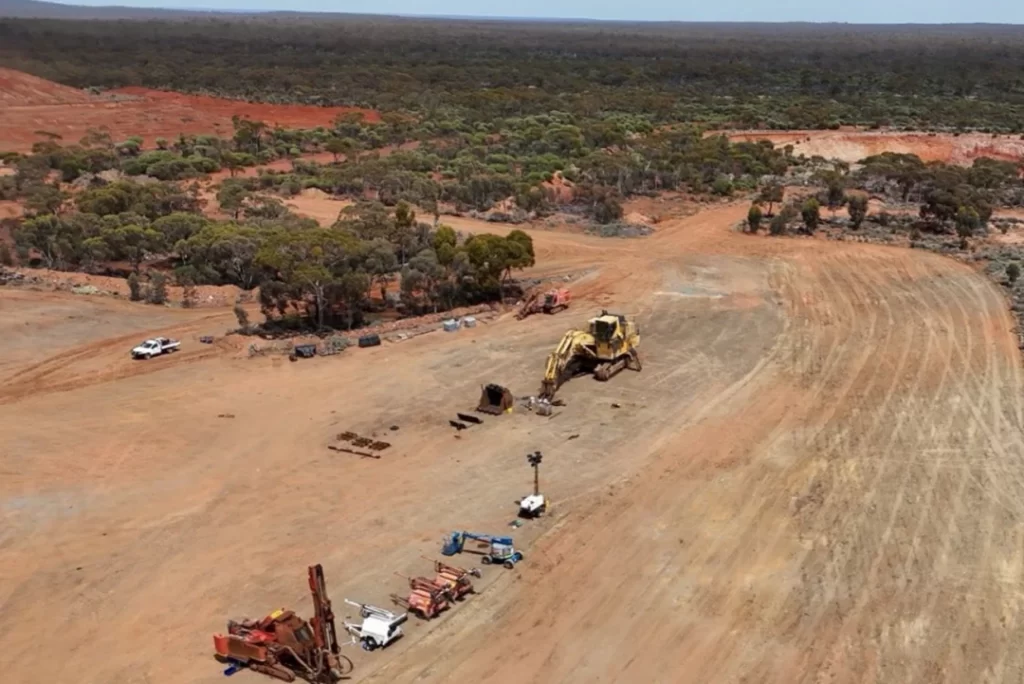
Common Antimony Ore Types & Processing Implications:
Ore Type Category | Common Minerals | Key Processing Considerations | Associated Elements & Challenges |
---|---|---|---|
Sulfide Ore | Stibnite (Sb2S3) – Most common primary mineral. | Mainly treated by froth Flotation Machine for concentration. Stibnite is very soft and easily crushed into fine mud (slimes). This needs careful grinding and flotation control. | Often found with Gold, Pyrite (Iron Sulfide), and Arsenopyrite (Arsenic Sulfide). Separating arsenic is a major challenge. |
Oxide Ores | Cervantite (Sb2O4), Stibiconite (Sb3O6(OH)), Valentinite/Senarmontite (Sb2O3) | Usually cannot be floated. Often need direct smelting or special leaching methods. Gravity separation might work if particles are coarse. | Can contain some leftover sulfides. Mineral structure can be complex. |
Complex/Mixed Ores | Mixes of sulfides, oxides, sulfo-salts (like Tetrahedrite with Sb). | Need complex, often custom-made processing plans. Might use flotation, gravity, leaching, and smelting steps one after another. Process choice depends heavily on all valuable and harmful elements present. | Highly variable. Arsenic is a very common and serious problem. Recovery of associated Gold, Silver, Lead, or Tungsten is often needed for the project to make money. |
Antimonial Lead Ores | Antimony often found with Galena (Lead Sulfide). | Flotation circuits aim to separate lead and antimony sulfides. Smelting often focuses on lead production. Antimony is recovered as a byproduct. | Lead is the main value here. Antimony recovery is secondary. |
Understanding your ore’s mineralogy – not just the antimony minerals but also the gangue (waste rock) and crucially, the associated valuable (Gold) and problematic (Arsenic) elements – is the absolute foundation for designing an effective and economical processing plant.
What Core Steps Does a Typical Antimony Processing Flow Include?
A typical flow involves these main steps: 1. Size Reduction using Crushing Equipment and Grinding Mills. 2. Beneficiation, which means concentrating the antimony minerals, often with a Flotation Machine or Gravity methods. 3. Extraction, using Smelting or Leaching to get crude antimony or oxide. 4. Refining, which purifies the product to meet final quality standards.
The Main Sequence of Processing/Core Antimony Processing Stages:
Stage | Purpose | Common Methods/Equipment | Key Considerations |
---|---|---|---|
1. Size Reduction | Break the ore and grind it fine enough to free the antimony minerals from the waste rock. | [Jaw Crusher], [Cone Crusher], [Impact Crusher]; Grinding Mills (Ball Mill, Rod Mill). | Very important for Stibnite: Avoid grinding too fine because it’s very soft and brittle. The target size depends on when minerals become free (liberation size). |
2. Beneficiation | Physically separate and concentrate the valuable antimony minerals. Throw away the waste rock. Increase the antimony grade. | Flotation Machine (most common for Stibnite), Gravity Separation (Jigging Separator Machine, Shaking Table, Spirals). | Choice depends on ore type (Flotation for sulfides, Gravity might work for both if particles are coarse). Big challenge: Separating antimony from Arsenic minerals. |
3. Extraction | Chemically remove antimony from the concentrate. Produce a crude metal or an intermediate compound like oxide. | Pyrometallurgy (Smelting/Volatilization) is the most common way. Hydrometallurgy (Leaching) is used in some specific cases. | Smelting needs very high temperatures. Antimony compounds turn into gas easily, requiring excellent gas and dust handling systems. Leaching has problems with selectivity and purification. |
4. Refining | Purify the crude antimony metal or intermediate oxide. Make it pure enough to meet final market quality rules. | Pyrometallurgical refining (using fluxes), Electrolytic refining (for very high purity metal), Sublimation or Chemical methods for Sb2O3. | Remove final impurities like Arsenic, Iron, Lead, Sulfur to get the desired quality (e.g., 99.65% Sb metal, specific Sb2O3 quality). |
Each stage needs specific equipment. Each stage needs careful control during operation. Success comes from optimizing every step. You must also consider how the steps connect, especially the links between grinding (liberation), concentration (flotation/gravity), and extraction.
How to Efficiently Concentrate Stibnite via Flotation, Tackling Sliming and Liberation Issues?
Good stibnite flotation needs several things. First, minimize slime creation by carefully controlling grinding in stages. Second, use specific, selective chemicals (reagents). Third, often use gravity separation early on to recover coarse, liberated stibnite.
flotation machine work principle
Overcoming Stibnite Flotation Difficulties
Stibnite (Sb2S3) has unique problems in flotation:
- The Slime Problem: Stibnite is extremely soft (Mohs hardness 2). It’s also brittle and breaks easily along flat planes. Normal grinding methods used for harder minerals will quickly turn it into excessive ultra-fine particles (smaller than 10 microns). These “slimes” are very hard to float effectively. They can also coat other mineral particles. This harms the whole flotation process and wastes chemicals.
- Solution: Use multi-stage grinding. Use efficient classifiers like Hydrocyclones or Spiral Classifiers to remove particles as soon as they are the right size. Consider using gentler grinding mills like a Rod Mill or adjusting Ball Mill conditions. Don’t use too much grinding energy.
- Using Gravity First: Stibnite is quite dense (about 4.6 g/cm³). Common waste minerals like quartz are much lighter (about 2.7 g/cm³). This density difference makes gravity separation work very well, especially for larger particles.
- Solution: Add gravity separation equipment like a Jigging Separator Machine, Shaking Table, or Spiral Chute before fine grinding. Or put it inside the grinding circuit (for example, treating the coarse material from the classifier). This recovers coarse stibnite early. It stops it from being ground too fine and lost as slime in flotation. It also reduces the amount of material going to the flotation circuit. Sometimes it can even produce a final coarse product directly.
- Sensitive Chemicals: Stibnite flotation needs very precise control of chemical reagents. There is no single “magic recipe.”
- Collectors: Often uses combinations like kerosene plus ester-type collectors. Or it uses special sulfur-based collectors (like thiols or xanthates, but conditions must be right).
- pH Control: Usually needs neutral to slightly alkaline conditions (pH 7-9). Soda ash is often used to control pH. Lime is usually avoided because high pH can stop stibnite from floating.
- Depressants: These chemicals are vital for separating stibnite from unwanted minerals, especially pyrite (iron sulfide) and arsenopyrite (arsenic sulfide). Sodium silicate (water glass) helps suppress silicate waste minerals. Special depressants (like starch, dextrin, or other chemicals) might be needed for pyrite and arsenopyrite. But finding chemicals and conditions that suppress these without suppressing stibnite needs a lot of testing and fine-tuning.
Success needs detailed knowledge of the ore minerals. It needs many lab tests to find the best grinding plan and chemical recipe. It also needs good process control in the plant using reliable Flotation Machines.
Pyrometallurgy is Mainstream: What Key Smelting or Volatilization Techniques Extract Antimony? (Which Suits My Ore?)
Direct smelting, often in a blast furnace, produces crude antimony metal. This works best for higher-grade materials. Volatilization methods, like roasting or fuming in kilns or furnaces, produce antimony trioxide (Sb2O3) dust. These can handle lower-grade or complex materials. The best choice depends on your feed grade, the product you want, and the impurities present.
Rotary Kiln
Picking the Correct Fire-Based Method
Pyrometallurgy is the main method for primary antimony production. Key Antimony Pyrometallurgical Routes:
Technique | Process Description | Primary Product | Feed Suitability | Key Challenges & Considerations |
---|---|---|---|---|
Direct Smelting | Melting the concentrate with fluxes and reducing agents (like coke) in furnaces (e.g., blast furnace). This directly produces liquid crude antimony metal. | Crude Antimony Metal | Higher-grade concentrates or lump ores (usually over 45-50% Sb). | Needs good quality feed. Creates slag waste that contains some lost antimony. Uses a lot of energy. Makes a lot of flue dust that must be captured. |
Volatilization Roasting/Fuming | Heating the concentrate or ore (often with controlled air/oxygen) in furnaces (like rotary kilns). This turns antimony into Sb2O3 gas, which is then collected as fine dust. | Antimony Trioxide (Sb2O3) Dust | Lower-grade concentrates, complex ores, oxide ores, materials with many impurities (like Arsenic). Can be designed to evaporate Sb away from other metals. | High Volatility Problem : Antimony compounds easily turn into gas at high temperatures. Needs very efficient gas cooling and dust collection systems (like baghouses, ESPs) to recover antimony and prevent pollution. Creates large amounts of gas needing treatment (SO2, Arsenic removal). |
Matte Smelting | Sometimes used for complex ores containing copper and antimony or lead and antimony. Produces an intermediate “matte” mixture needing more processing. | Intermediate Matte | Complex sulfide concentrates that also contain other valuable metals. | Needs a more complicated process flow with extra steps like converting and refining. |
The Big Challenge: Volatility and Pollution
No matter which fire method you use, the high volatility of antimony compounds is a huge factor. Antimony oxides and sulfides easily turn into gas at high temperatures.
- Recovery Losses: A lot of antimony can escape as gas if it’s not captured properly.
- Environmental Problems: The dust created (flue dust) is often full of antimony. It also contains hazardous impurities like arsenic and lead. If the feed contains sulfur, toxic sulfur dioxide (SO2) gas is also produced.
- Expensive Gas Cleaning: Effective pyrometallurgy absolutely requires large and expensive gas handling systems. This includes cooling systems, high-efficiency dust collectors (baghouses, electrostatic precipitators), and systems to remove SO2 and possibly arsenic from the exhaust gas. This equipment is a major part of the plant’s cost to build and run.
While wet methods (hydrometallurgy) exist, they often have their own issues. These include problems with selectively dissolving only antimony, needing complex purification steps, and dealing with wastewater. This means pyrometallurgy, even with its gas handling needs, is still the most common method.
How is Crude Antimony Refined to Meet Different Grade Requirements or High-Purity Oxide Specs?
Crude antimony metal is usually refined using pyrometallurgical methods. This involves adding specific chemicals (fluxes) to remove impurities like arsenic, iron, and sulfur. Electrolytic refining is used to make ultra-high purity metal. Antimony trioxide needs separate purification, often involving re-volatilization (sublimation).
different antimony
Reaching Final Product Quality
Refining removes the remaining impurities. This achieves the target quality needed for different applications:antimony Refining Methods:
Method | Process Description | Target Product | Impurities Removed Effectively | Key Considerations |
---|---|---|---|---|
Pyrometallurgical Refining (Metal) | Melt crude antimony. Add specific fluxes (like caustic soda, sodium nitrate, soda ash) under controlled conditions. Impurities react and form a slag layer that is removed. | Standard Grade Sb Metal (~99.65%) | As, S, Fe, Cu, sometimes Pb. | Most common method. Relatively low cost. May need multiple steps depending on impurity levels. Creates slag waste. |
Electrolytic Refining (Metal) | Dissolve less pure antimony (anode) in a special acid solution (electrolyte). Pure antimony plates onto a cathode using electricity. | High Purity Sb Metal (>99.9% to >99.999%) | Most metallic impurities. | Higher cost, more complex process. Needed for making semiconductors and special alloys. The electrolyte needs careful handling. |
Sublimation (Oxide) | Heat crude antimony trioxide dust under controlled conditions. The Sb2O3 turns into gas (sublimes) and is collected again as pure solid, leaving less volatile impurities behind. | High Purity Sb2O3 | Fe, Pb, non-volatile oxides. | Good for upgrading technical grade oxide. Needs careful control of temperature and atmosphere. |
Chemical Purification (Oxide) | Dissolve crude oxide in specific chemicals. Purify the solution. Then precipitate pure Sb2O3 or an intermediate salt, which is converted to pure oxide. | High Purity Sb2O3 | Wide range, depends on process | Can make very pure oxide. But involves wet chemistry steps. Can be more expensive. Creates liquid waste to treat. |
The best refining method depends entirely on the starting material’s impurities. It also depends on the quality needed for the final product. Standard grade metal for alloys might just need pyro-refining. But antimony trioxide for flame retardants often needs sublimation or chemical methods to meet very strict purity and particle size rules.
How is Troublesome Arsenic Handled? What Other Environmental Hurdles (like SO2) Must Be Overcome in Antimony Smelting?
Managing arsenic needs action at multiple stages. Maximize its removal during beneficiation (concentration). Control its behavior during smelting (often fixing it in stable waste slag or dust). Capture arsenic-rich dust securely. Treat any water containing arsenic. Sulfur dioxide (SO2) gas must be captured using scrubbing systems.
Dealing with Environmental Problems
Antimony processing, especially using fire methods (pyrometallurgy), creates major environmental challenges. These must be managed for the plant to operate sustainably:
- The Arsenic Challenge:
- Common and Difficult: Arsenic (often as the mineral Arsenopyrite) is frequently found with antimony ores. It behaves similarly to antimony chemically. This makes it hard to separate during flotation.
- Behavior in Smelting: During smelting, arsenic tends to turn into gas along with antimony. This contaminates the flue dust. Or, it can end up in the slag waste, making it hazardous.
- Management Strategies:
- Beneficiation: Try to remove as much arsenic as possible into the waste tailings during flotation by optimizing the process.
- Smelting Control: Choose smelting conditions that either lock the arsenic into a stable slag form (like calcium ferrite) or concentrate it into specific dust streams. These streams can then be treated separately and safely.
- Dust Handling: It is critical to capture all the flue dust very efficiently. Dusts high in arsenic need special handling and disposal. Often, they must be chemically stabilized to make the arsenic less likely to dissolve before being put in special secure landfills.
- Hydrometallurgy: If wet methods are used, arsenic dissolves into the solution. This requires complex purification steps (like precipitating it as stable ferric arsenate) and careful wastewater treatment.
- Cost Impact: Dealing with arsenic (treatment and safe disposal) is a very large operating cost and long-term environmental risk. It can decide if a project makes money or not. Checking the arsenic content and how it exists in the ore early on is extremely important.
- Sulfur Dioxide (SO2) Emissions:
- Source: Roasting or smelting sulfide concentrates (like Stibnite, Pyrite, Arsenopyrite) releases large amounts of SO2 gas.
- Control: Environmental laws demand very low SO2 emissions. Plants must install gas scrubbing systems. These usually convert the SO2 into sulfuric acid (if it can be sold nearby) or neutralize it to form gypsum (calcium sulfate) for disposal. These systems add significant cost to building and running the plant.
- Other Dusts and Wastes:
- General dust control is needed everywhere in the plant (e.g., [Crushing Equipment], conveyors, mills).
- Slag waste from smelting needs testing to ensure it’s stable and won’t leach metals before disposal or possible reuse.
- Wastewater from different parts of the plant needs treatment to remove metals and fine solids.
Modern antimony processing plants must include comprehensive environmental control systems. These are essential parts of the operation, not optional extras.
How Can Associated Gold or Other Valuable Metals in Antimony Ore Be Recovered Comprehensively?
Comprehensive recovery means designing the processing plan specifically to capture byproducts, especially gold. This might involve adding separate circuits just for gold recovery (like flotation or cyanidation). It could mean changing the antimony flotation process. Or it could mean using smelting methods that collect precious metals.
gold dore bar, silver granules, antimony metal ingots
Getting Maximum Value from Complex Ores
Ignoring valuable byproducts is a huge economic mistake. This is especially true for gold, which is often the main source of value in gold-antimony deposits.
Strategies for Comprehensive Recovery (Focus on Gold):
Strategy Approach | Description | Key Considerations |
---|---|---|
1. Gold Recovery First | Float or leach gold (e.g., using cyanide) from the ore before processing the antimony. | Best if gold is easily freed and recovered without causing problems for later antimony processing. Avoids trapping gold in the antimony concentrate if the antimony smelting method doesn’t recover gold well. Needs a separate gold recovery circuit. |
2. Sequential Flotation | Design the Flotation Machine circuit to first float a concentrate rich in gold (maybe with pyrite/arsenopyrite). Then float the antimony (stibnite). | Needs minerals that behave differently enough to allow selective flotation. Requires complex chemical (reagent) schemes. Managing arsenic is key. |
3. Antimony Recovery First, then Gold | Float the antimony concentrate first. Then treat the leftover waste material (tailings) from flotation to recover the gold (usually with cyanide leaching). | A common method. Makes sure antimony is recovered. Gold recovery depends on how much is left in the tailings and if it can be leached easily. Need to ensure antimony flotation chemicals don’t harm the later gold leaching step. |
4. Bulk Sulfide Flotation, then Separation | Float all valuable sulfide minerals together (gold-bearing pyrite/arsenopyrite, stibnite). Then use more flotation or wet chemical methods to separate them. | Can get high initial recovery of everything. But needs complex separation steps later. |
5. Smelting Routes Capturing Gold | Use fire-based processes (like lead or copper smelting if those metals are present, or use special fluxes) where gold collects in the molten metal (bullion) or intermediate matte phase along with antimony or other metals. | Needs specific smelting equipment. Gold must then be refined from the bullion or matte. How well it works depends heavily on the exact smelting chemistry and conditions. |
Thinking About Other Metals
- Silver (Ag): Often found with gold. Recovery methods are usually similar to gold.
- Lead (Pb): If present as Galena (lead sulfide), it’s typically recovered by selective flotation before or with antimony. Smelting often focuses on producing lead metal, with antimony as a byproduct.
- Tungsten (W): Sometimes found with antimony (e.g., Scheelite mineral). May need separate gravity circuits (Shaking Table) or flotation steps.
The best strategy depends entirely on the specific minerals in your ore. It depends on the metal grades, how they are mixed together, and how easily they can be separated. Detailed lab testing (metallurgical test work) is essential to design a plan that recovers the maximum value from all valuable components, not just antimony.
What Key Equipment is Needed for an Antimony Processing Production Line? (From Crushing to Smelting/Dust Collection)
Key equipment includes Crushing Equipment (like [Jaw Crusher], [Cone Crusher]), Grinding Mills (Ball Mill), Classifiers, Flotation Machines or Gravity Separators (Jigs, Tables), Thickeners, Filters, Smelting Furnaces or Roasting Kilns, Refining Kettles or Cells. Very importantly, it also includes large Dust Collection systems (baghouses, ESPs) and Gas Scrubbing systems.
ZONEDINGMACHINE
Core Machines for the Antimony Flowsheet
An antimony processing line combines various types of equipment. Many of these are available from ZONEDING.Essential Equipment by Process Stage:
Process Stage | Key Equipment Types | ZONEDING Examples | Function |
---|---|---|---|
1. Comminution (Size Reduction) | Primary Crusher, Secondary/Tertiary Crushers, Grinding Mills, Classifiers (Hydrocyclone/Spiral Classifier) | Jaw Crusher, Cone Crusher, Impact Crusher, Ball Mill, Rod Mill, Hydrocyclone, Spiral Classifier | Breaking ore down to the size where minerals are freed (liberation size). Needs careful control for soft Stibnite. |
2. Beneficiation (Concentration) | Flotation Machines, Conditioners (Mixer tanks), Reagent Feeders; Gravity Separators | Flotation Machine, Mixer; Jigging Separator Machine, Shaking Table, Spiral Chute | Separating valuable antimony minerals from waste rock. Flotation for sulfides; Gravity might be very important. |
3. Dewatering | Thickeners, Filters (e.g., Filter Press, Vacuum Filter) | High Efficiency Concentrator (similar function to thickeners) | Removing water from the concentrate before smelting. Removing water from tailings waste before disposal. |
4. Extraction (Pyrometallurgy) | Roasting Kilns (e.g., Rotary Kiln), Smelting Furnaces (e.g., Blast Furnace, Electric Furnace, reverberatory), Converters, Ladles | (ZONEDING mainly focuses on the earlier mineral processing stages. Partners can supply downstream equipment.) | Extracting antimony from concentrate using high heat. Needs strong equipment that can handle high temperatures. |
5. Refining | Refining Kettles/Furnaces, Electrolytic Cells, Casting Equipment | (Downstream equipment) | Purifying crude antimony metal or oxide to final quality standards. |
6. Environmental Control (CRITICAL) | Dust Collectors (Baghouses, Electrostatic Precipitators – ESPs), Gas Scrubbers (for SO2, possibly As), Wastewater Treatment Plant components | (These are vital support systems. Specialized companies often supply them alongside the main processing equipment.) | Capturing harmful dusts (containing Sb, As) and gases (like SO2) to meet laws and recover valuable material. Treating water. |
Building a complete antimony processing line means putting together equipment for all these stages. It is essential to choose strong, reliable machines. They must be suitable for the specific challenges of antimony ores. These challenges include softness, abrasiveness, potential corrosion, high temperatures, and lots of dust generation.
What Capabilities and Experience Should Be Prioritized When Choosing Antimony Processing Technology and Equipment Suppliers?
Focus on suppliers with proven experience. They should have experience specifically with antimony ores or similar complex sulfide ores. This includes experience with flotation of soft minerals, managing arsenic, or recovering gold. Check their ability to customize equipment. Ensure they provide robust machinery. See if they offer process knowledge. And confirm they deliver strong after-sales support.
zoneding team
Picking the Right Partner for a Difficult Ore
Antimony is not a simple commodity. Choose your partners very carefully:
- Proven Relevant Experience: ZONEDINGMACHINE provided equipment (like Flotation Machines, Ball Mills, Crushing Equipment) for plants that successfully process antimony ores. And ores with challenges similar to yours (e.g., high arsenic, associated gold, fine grinding needs). ZONEDING can offe specific examples (case studies) and customer references. ZONEDING’s broad experience across many mineral types provides a solid foundation.
- Customization Ability: Antimony ores are very different from each other. ZONEDINGMACHINE can adjust equipment designs for your specific needs. For example, ZONEDING provides special mill linings for abrasive ore, and configure flotation cells for fine particle recovery and can use materials that resist corrosion. ZONEDING highlights its ability to customize solutions.
- Understanding Antimony Challenges: ZONEDINGMACHINE can understand the problems. ZONEDINGMACHINE knows about stibnite’s softness, recognizes the potential need for gravity circuits, understands the sensitivity of flotation chemicals, and knows the critical importance of dust control. ZONEDING technical team has this knowledge.
- Equipment Strength and Reliability: Processing plants run constantly in tough conditions.Look for high-quality manufacturing and suitable materials.ZONEDINGMACHINE equipment is durable and reliable to avoid costly downtime.
- Process Integration and Flowsheet Support: ZONEDINGMACHINE can offer complete packages (like crushing, grinding, flotation together), and understand how their equipment fits into the whole plant design and affects overall performance. ZONEDING offers complete production lines.
- After-Sales Support: This is crucial for keeping the plant running long-term. ZONEDINGMACHINE has ability to provide technical help, troubleshooting assistance, readily available spare parts, and local service support.
- Focus on Environmental Aspects: ZONEDINGMACHINE offers equipment designed for efficiency (using less energy and water), understands the need to connect their equipment with environmental control systems.
Partnering with an experienced and reputable supplier like ZONEDING, who understands the intricacies of mineral processing and offers robust, customized equipment backed by reliable support, is essential for the long-term success of your cobalt operation.
Conclusion
Processing antimony ore is complex but possible with the right plan. Success depends on knowing your ore, managing gold and arsenic, choosing suitable technology, and working with experienced suppliers like ZONEDING.
Related notes
What is a Ball Mill Used For?
How to choose magnesium ore ball mill? The role and advantages of magnesium ore ball mill
Iron Fine Powder Ball Mill Application Scope
Phosphate ball mill working principle, structure, phosphate ball mill steel ball loading capacity
Should I use a ball mill or a rod mill to grind limestone?
Lithium pyroxene ball mill features, lithium ore ball mill price
loading…
已经是到最后一篇内容了!
Related Products
Ball Mill
Our ball mill are available in different styles and many models in each style to adapt to various grinding requirements.
Rod Mill
Rod MillRod Mill For SaleWorking Principle of Rod MillProduct Features of Rod MillRod Mill shipmentParameters of Rod MillRod millService Supportof Rod MillFAQRelated ProductsOur Rod Mill are available in different styles and numerous model sizes …
Ceramic Ball Mill
Ceramic Ball MillCeramic ball mill For SaleAdvantages of Ceramic ball millFunctional Advantages of Ceramic ball millApplication Scenarios of Ceramic ball millCeramic ball mill shipmentCeramic ball mill customer work siteParameters of Ceramic ball…
Flotation Machine
Flotation MachineFlotation Machine For SaleAdvantages of Flotation MachineFlotation Machine: Suitable Ore TypesStructure of flotation machinePrinciple of Flotation MachineFlotation ProcessParameters of Flotation Machineflotation machineAssembly s…
Spiral Classifier
Spiral classifiers can grade different particles in ore slurry during the metal beneficiation process as well as deslime and dehydrate in the washing operation.
Mixer
Introduction of MixerThe Application and Function of Agitating TankThe Working Principle of Agitating TankAgitating Tank ManufacturerGeneral SpecificationMixerFAQRelated Products Mixer Mixing barrel is mainly used in all kinds of metal mining in…
Wet Drum Magnetic Separator
Wet Drum Magnetic SeparatorWhat is wet drum magnetic separatorFeatures of Wet Drum Magnetic Separator:Structure of Wet Drum Magnetic SeparatorPrinciple of Wet Drum Magnetic SeparatorCustomer Case of Wet Drum Magnetic SeparatorSpecification of Wet…
Shaking Table
Shaking Table For SaleAdvantages of Shaking TableApplication of Shaking TablePrinciple and structure of shaking tableI. Working PrincipleII. Structural compositionParameters of shaking tableShaking Tableshaking table customer work siteFAQRelated P…
Gold Mine Wet Pan Mill
Wet Pan Mill for saleApplicationsWet Pan Mill AdvantagesProduct StructureWet Pan Mill Working PrincipleParameters of Wet Pan MillRelated Products Gold Mine Wet Pan Mill is a highly efficient, energy-saving and easy-to-ope…
Jigging Separator Machine
Jigging Machine for saleApplicationsProduct StructureWorking PrincipleParameters of Jigging MachineJigging Machine customer work siteRelated Products Jigging Machine(jig concentrator, jig machine, mineral jig, Jiggin…
loading…
已经是到最后一篇内容了!
We use cookies to ensure that we give you the best experience on our website. If you continue to use this site we will assume that you are happy with it.
OK
Privacy Policy