Spiral Classifier
What is a spiral classifier?
The spiral classifier is a device that utilizes the principle of different sedimentation speeds of solid particles in a liquid based on their specific gravity for mechanical classification. It is widely used in closed-circuit processes in conjunction with ball mills to separate and classify ore sand in mining plants. It can also be applied in gravity separation plants for classifying ore sand and fine mud, as well as in metal ore dressing processes for size classification of ore pulp. Additionally, it finds application in de-sliming and dewatering operations during ore washing.
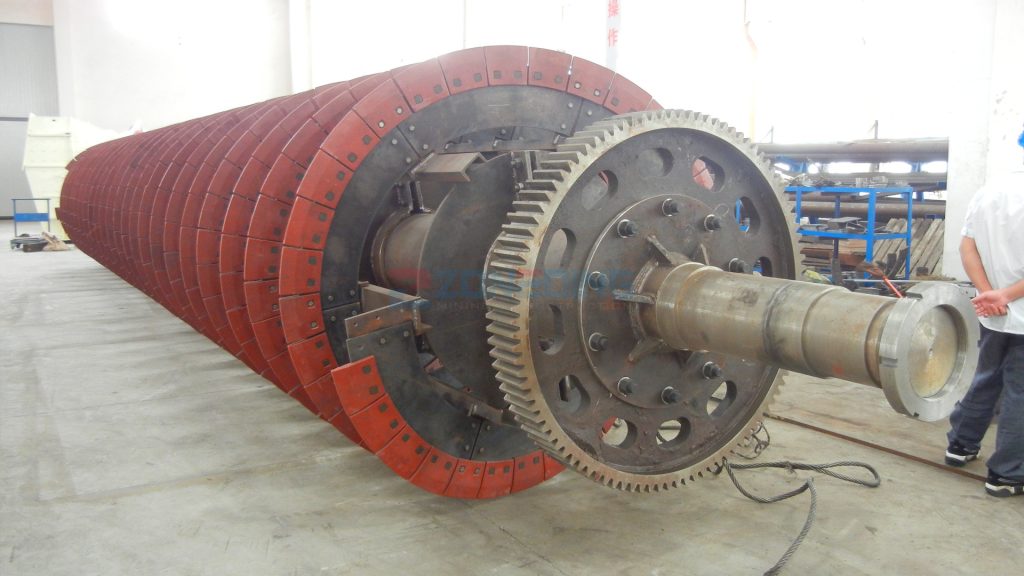

Types: There are four classifiers: high weir single spiral and double spiral, submerged single spiral and double spiral.
- High weir spiral classifier is suitable for coarse particle classification, the maximum size of overflow is generally 0.4~0.15mm;
- Submerged spiral classifier is suitable for fine particle classification, the maximum size of overflow is generally below 0.2mm.
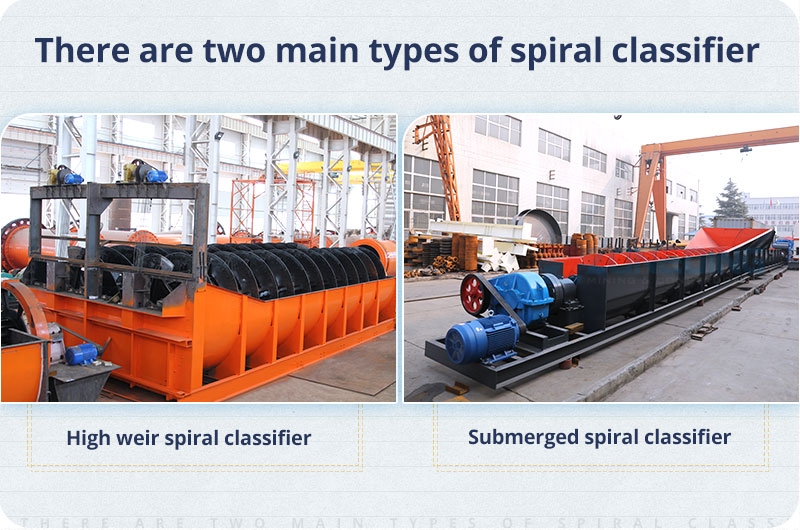
Applications of Spiral Classifier
- Mining Plants: Used in conjunction with ball mills to form a closed-circuit for ore sand separation and classification.
- Gravity Separation: Applied for classifying ore sand and fine mud to enhance mining efficiency.
- Metal Ore Dressing: Used in the ore dressing process for size classification of ore pulp to meet subsequent process requirements.
- Ore Washing Operations: Involved in de-sliming and dewatering processes during ore cleaning.
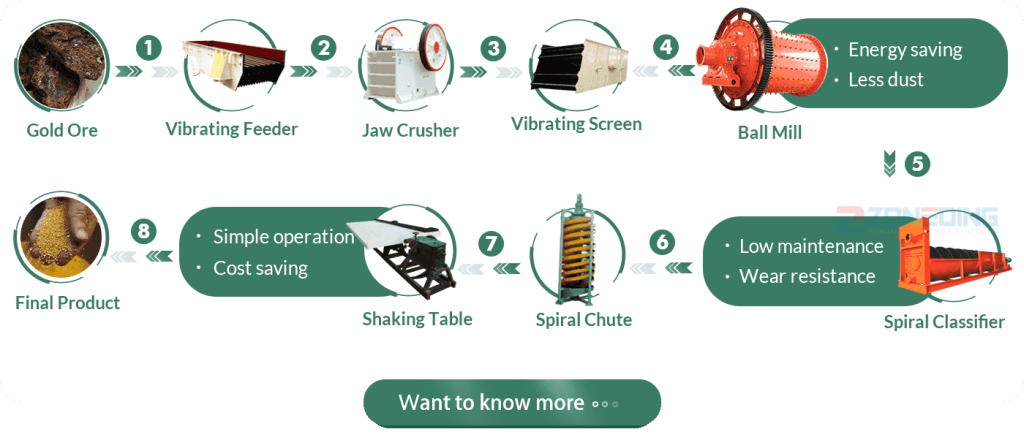
Advantages Of Spiral Classifier
- The energy consumption of spiral classifier is 50% lower than other classification equipment, and the output is also increased by 50%.
- The water tank has a large slope, which is convenient for forming a closed-circuit ring grinding operation with the ball mill, and forms a self-flow sand return.
- Simple operating process and stable working status, greatly reducing maintenance costs.
- Its spiral structure can ensure a large enough settling area to extend the material suspension time, which is more conducive to the even distribution of materials during the classification process.
- Users can adjust the parameters of the spiral classifier according to their needs, such as spiral speed, inclination and outlet size to achieve different classification requirements.
Principle of Spiral Classifier
The working principle of the spiral classifier is based on the different sedimentation speeds of solid particles in a liquid due to their varying specific gravities. When the ore pulp enters the tank from the side feed inlet, it forms a sedimentation zone at the bottom of the tank. The slowly rotating spiral provides a certain degree of agitation to the pulp. After agitation, the light and fine particles suspend on the surface, forming an overflow that flows over the weir at the end of the water tank into the next mineral processing step. The heavy and coarse particles settle at the bottom of the tank, forming a return sand that is transported by the spiral to the discharge port for removal, thus achieving the desired classification.
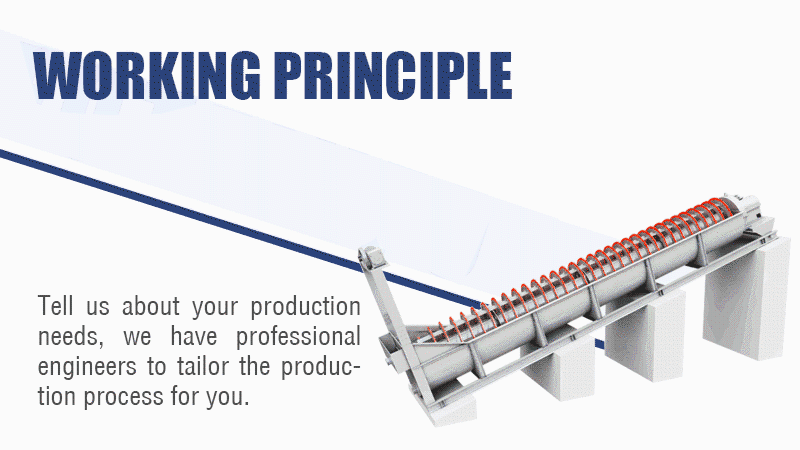
Structure of Spiral Classifier
The spiral classifier mainly consists of the following components:
- Transmission Device: Includes an electric motor, reducer, cylindrical gear pair, and bevel gear, responsible for driving the rotation of the spiral.
- Spiral Body: Composed of a hollow shaft, supports, spiral blades, and lining iron, which is the main working part of the classifier.
- Tank: Holds the entire slurry and bears the weight of the machine and all its loads. Constructed by welding steel plates and various steel sections.
- Lifting Mechanism: Used to raise or lower the spiral for maintenance or to adjust the processing level within the tank.
- Lower Bearing (Bushing): Supports the spiral and bears the load during operation.
- Discharge Valve: Located at the bottom of the tank, allowing the slurry to be drained when necessary.

General Specification
Spiral Classifier
Model | Spiral Diameter (mm) | Trough Length (mm) | Spiral rotate speed (r/min) | Processing capacity(t/d) | Motor Power(kw) | Dimensions(mm≤) | Total weight (t) | ||||
Sand -return | Overflow | For driving | For lifting | Length | Width | Height | |||||
FG-3 | 300 | 3000 | 12-30 | 80-150 | 20 | 1.1 | —- | 3850 | 490 | 1140 | 0.7 |
FG-5 | 500 | 4500 | 8-12.5 | 135-210 | 32 | 1.1 | —- | 5430 | 680 | 1480 | 1.9 |
FG-7 | 750 | 5500 | 6-10 | 340-570 | 65 | 3 | —- | 6720 | 980 | 1820 | 3.1 |
FG-10 | 1000 | 6500 | 5-8 | 675-1080 | 110 | 5.5 | —- | 7590 | 1240 | 2380 | 4.9 |
FC-10 | 8400 | 675-1080 | 85 | 7.5 | —- | 9600 | 1240 | 2680 | 6.2 | ||
FG-12 | 1200 | 6500 | 4-6 | 1170-1870 | 155 | 7.5 | 2.2 | 8180 | 1570 | 3110 | 8.5 |
FC-12 | 8400 | 1170-1870 | 120 | 7.5 | 2.2 | 10370 | 1540 | 3920 | 11 | ||
2FG-12 | 6500 | 2340-3740 | 310 | 15 | 4.4 | 8230 | 2790 | 3110 | 15.8 | ||
2FC-12 | 8400 | 2340-3740 | 240 | 15 | 4.4 | 10370 | 2790 | 3920 | 17.6 | ||
FG-15 | 1500 | 8300 | 4-6 | 1830-2740 | 235 | 7.5 | 2.2 | 10410 | 1880 | 4080 | 12.5 |
FC-15 | 10500 | 1830-2740 | 185 | 7.5 | 2.2 | 12670 | 1820 | 4890 | 16.8 | ||
2FG-15 | 8300 | 2280-5480 | 470 | 15 | 4.4 | 10410 | 3390 | 4080 | 22.1 | ||
2FC-15 | 10500 | 2280-5480 | 370 | 15 | 4.4 | 12670 | 3370 | 4890 | 30.7 | ||
FG-20 | 2000 | 8400 | 3.6-5.5 | 3290-5940 | 400 | 11-15 | 3 | 10790 | 2530 | 4490 | 20.5 |
FC-20 | 12900 | 3210-5940 | 320 | 11-15 | 3 | 15610 | 2530 | 5340 | 28.5 | ||
2FG-20 | 8400 | 7780-11880 | 800 | 22-30 | 6 | 11000 | 4600 | 4490 | 35.5 | ||
2FC-20 | 12900 | 7780-11880 | 640 | 22-30 | 6 | 15760 | 4600 | 5640 | 48.7 | ||
FG-24 | 2400 | 9130 | 3.67 | 6800 | 580 | 15 | 3 | 11650 | 2910 | 4970 | 26.8 |
FC-24 | 14130 | 6800 | 490 | 18.5 | 4 | 16580 | 2930 | 7190 | 41 | ||
2FG-24 | 9130 | 13600 | 1160 | 30 | 6 | 12710 | 5430 | 5690 | 45.8 | ||
2FC-24 | 14130 | 13700 | 910 | 37 | 8 | 17710 | 5430 | 8000 | 67.9 | ||
2FG-30 | 3000 | 12500 | 3.2 | 23300 | 1785 | 40 | 8 | 16020 | 6640 | 6350 | 73 |
2FC-30 | 14300 | 23300 | 1410 | —- | —- | 17091 | —- | 8680 | 84.8 |
FAQ
1.Are you a manufacturing or trading company?
We are manufacturer. Our factory established in 2004.
2.What is the after-service of your company?
We can provide the foundation drawing, installation service, training, spare parts and other service according to the customer’s requirements.
3. Which mineral processing method should I choose?
According to the properties of minerals, we will choose the treatment method that most suitable for you.
4. What machines are usually required for the whole production line?
Usually there are feeder, primary and secondary crushers, vibrating screen, ball mill, classifier, spiral chute, magnetic or flotation machine, dryer, etc. Equipment can be adjusted.
5. What is the final mineral concentration?
It depends on the ore grade. The final concentration of gold ore can reach 80-90%.
Related Products
Ball Mill
Our ball mill are available in different styles and many models in each style to adapt to various grinding requirements.
Rod Mill
Rod MillRod Mill For SaleWorking Principle of Rod MillProduct Features of Rod MillRod Mill shipmentParameters of Rod MillRod millService Supportof Rod MillFAQRelated ProductsOur Rod Mill are available in different styles and numerous model sizes …
Ceramic Ball Mill
Ceramic Ball MillCeramic ball mill For SaleAdvantages of Ceramic ball millFunctional Advantages of Ceramic ball millApplication Scenarios of Ceramic ball millCeramic ball mill shipmentCeramic ball mill customer work siteParameters of Ceramic ball…
Flotation Machine
Flotation MachineFlotation Machine For SaleAdvantages of Flotation MachineFlotation Machine: Suitable Ore TypesStructure of flotation machinePrinciple of Flotation MachineFlotation ProcessParameters of Flotation Machineflotation machineAssembly s…
Mixer
Introduction of MixerThe Application and Function of Agitating TankThe Working Principle of Agitating TankAgitating Tank ManufacturerGeneral SpecificationMixerFAQRelated Products Mixer Mixing barrel is mainly used in all kinds of metal mining in…
Wet Drum Magnetic Separator
Wet Drum Magnetic SeparatorWhat is wet drum magnetic separatorFeatures of Wet Drum Magnetic Separator:Structure of Wet Drum Magnetic SeparatorPrinciple of Wet Drum Magnetic SeparatorCustomer Case of Wet Drum Magnetic SeparatorSpecification of Wet…
Shaking Table
Shaking Table For SaleAdvantages of Shaking TableApplication of Shaking TablePrinciple and structure of shaking tableI. Working PrincipleII. Structural compositionParameters of shaking tableShaking Tableshaking table customer work siteFAQRelated P…
Gold Mine Wet Pan Mill
Wet Pan Mill for saleApplicationsWet Pan Mill AdvantagesProduct StructureWet Pan Mill Working PrincipleParameters of Wet Pan MillRelated Products Gold Mine Wet Pan Mill is a highly efficient, energy-saving and easy-to-ope…
Jigging Separator Machine
Jigging Machine for saleApplicationsProduct StructureWorking PrincipleParameters of Jigging MachineJigging Machine customer work siteRelated Products Jigging Machine(jig concentrator, jig machine, mineral jig, Jiggin…
Hydrocyclone
Hydrocyclone Overview Figure 1. Schematic representation of the spiral flow. Figure 2. Principal features of a hydrocyclone. ,
loading…
已经是到最后一篇内容了!